For how I make my comm connections, I have had the best results by using either the carbon from inside an old-school zinc/carbon "C" sized battery (getting hard to find and a PITA to get out of there), or a copper-clad carbon welding rod like this:
"Arc Welding Rod, Gouging Carbon, Material Copper, Dia. 5/16 In., Length 12 In., Container Tube 10 pc"
Anyone know an online retailer (shopping cart type deal) where I can get them in a small quantity? The site I got the picture from doesn't do this.
-john
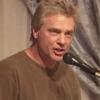
Brazing/welding rod
#1
Posted 21 July 2013 - 09:06 AM
#2
Posted 21 July 2013 - 09:22 AM
John,
Those are called gouging rods. McMaster has them in all diameters. As you can see, in packs of ten...
Rick Bennardo
"Professional Tinkerer"
scrgeo@comcast.net
R-Geo Products
LIKE my Facebook page for updates, new releases, and sales: Rgeo Slots...
Lead! The easy equalizer...
#3
Posted 21 July 2013 - 09:23 AM
#4
Posted 21 July 2013 - 09:31 AM
-john
#5
Posted 21 July 2013 - 10:14 AM
#6
Posted 21 July 2013 - 10:33 AM
I'm glad you found what you needed. McMaster-Carr is where I would have looked, too! I have a small order saved on their site right now.

Rick
Rick Thigpen
Check out Steve Okeefe's great web site at its new home here at Slotblog:
The Independent Scratchbuilder
There's much more to come...
#7
Posted 21 July 2013 - 11:04 AM
I'm glad you found what you needed. McMaster-Carr is where I would have looked, too! I have a small order saved on their site right now.
Yeah... it figures, eh Rick? They have just about everything else (except maybe an elephant ear on toast... and I have to admit I never checked, so maybe!)

What type of welder do you use to weld the comm wires, John?
Hi Paul.
I don't use a real welder. I use a 55amp car starter/battery charger. In "starter" mode, it will deliver up to the rated current all in one shot which is what you need for this. Using either a battery electrode or the carbon gouging rod as my positive (and the negative attached to the comm segment), you touch the carbon to the comm tab and then trip the car starter using a heavy duty momentary switch with your foot. The carbon heats up VERY fast (like a second or so) to where the brazing metal (in my case, jeweler's silver with a flow temp or around 1200F) will flow. It's a very simple rig that works very well, once you get the hang of it. Downsides are:
1) Keep the current on too long and you'll melt the comm copper as well as the brazing metal
2) Not touching the com tab squarely or solidly enough can result in striking an arc and vaporizing the tab as well as the copper magnet wire
3) Because the carbon is relatively soft material, you have to "tune up" the very tip of the carbon every couple of armatures to avoid #2.
4) There's a fair amount of practice involved before you start to get predictable/repeatable results, and your method has to change a little depending on whether you're working on "straight" or hooked comm tabs... and you have to be extra cautious when working on the really thin tabs on some motors like modern "D" motor comms. The brazing metal flows at a significantly lower temperature than copper will melt at, but with that much current, the time difference between what it takes to reach 1200F and then melting point of copper is not long at all.
-john
#8
Posted 21 July 2013 - 11:42 AM
Cool results though once you get the hang of it.

#10
Posted 14 December 2014 - 09:36 PM
A timer is a troublesome thing when brazing commutators. You have to make some split second decisions and a timer just gets in the way sometimes. I hard wired around mine and use a simple foot switch to fire my welder.
- havlicek likes this
#11
Posted 14 December 2014 - 11:38 PM
Yea, as I found a few more posts using the search function I found out he prefers to do a few short bursts instead of one solid one. Sounds like something a good size capacitor would be good for.
#12
Posted 15 December 2014 - 09:15 AM
In an industrial setting where you might do thousands of arms during a shift and they're all the same, certainly standardizing and automating things would be more desirable and feasible, however those are (all?) done by resistance welding and not brazing, and the two processes present different considerations. There are plenty of videos online showing automated and semi-automated (hand feed) resistance welding done on a turret fixture, and all three poles are done in a couple of seconds... by several different methods.
-john
#13
Posted 15 December 2014 - 12:24 PM
You may find less control using a capacitor, rather than a transformer style power source.
#14
Posted 15 December 2014 - 01:19 PM
Probably not so good for the "brazing" technique, would be more of a spot weld. Should be able to improve the precision with a micro-controller to control how often it fires it instead of trying to do it in one big shot.
#15
Posted 15 December 2014 - 01:46 PM
Yes, I have one of those welders purchased at enormous expense by former armature manufacturer Robert Root of RJR engineering. Basically a transformer style resistance welder but conrols everything - pulse timing, current, pulse count, pueumatic clamp mechanism, water cooled heat sink, makes espresso.
When I bought it, the choice was to put it in a dumpster or sell it to me - I won.
For all that, Dan Miller and John Havlicek have devised much simpler and less expensive means of getting that commutator tab to 1200 degrrees and melt the silver. Works every bit as well as the machine with all the bells and whistles. Especially in this procedure, the importance of the skill of the operator cannot be overstated.
#16
Posted 30 December 2014 - 08:13 AM
I should mention also that, at least with my crude method, the tip of the carbon electrode does need to be reformed/touched up every few arms. After reforming (I have a shape that works well for most com tabs), the electrode works noticeably better and faster and then starts to degrade a little until it needs re-forming. After a while, you need to completely reshape the tip from scratch. This, along with different tabs and gauges of wire, means you have to be on your toes and sort of "feel" what's happening so you can adjust your current pulses. Things can go south pretty fast if you stay on "auto pilot". There are other materials being used for this that *should* hold a tip shape longer (like tungsten rod), but I haven't had an success with them for some reason, so I stay with what works "for me".
The thing about brazing with mostly silver alloy as your filler metal is that the connections (when done right) are electrically and mechanically very sound. On average, I would think that they produce significantly better (electrically speaking) results than even automated resistance welding. I've seen arms jump to near perfect (or "perfect" within the range of the meter) meter from way out many many times. The silver fills micro gaps and of course, silver is the best conductor (at room temp) of any of the elements/metals...better than gold and certainly better than the copper coil wire you're connecting to the copper tabs.
-john
#18
Posted 26 January 2015 - 08:55 AM
#19
Posted 26 January 2015 - 09:07 AM
Those look great Robert! Looks like 6 keys per com segment, and slit "just" deep enough to leave a lot of meat in the phenolic. How's concentricity? I can see some very special arms coming in my crystal ball With a melting point of over 1700F (if the shells are pure silver), there's still plenty of safety room for brazing (copper is like 1900F). With "similar" hardness to copper (I think a bit harder), and unbeatable conductivity they should be very good for the application.
-john
#20
Posted 26 January 2015 - 09:13 AM
.999, .925, or .900 ?
Are you asking about the rod diameter David? Those are way-big so, probably not. Just in case, we're talking about roughly "pencil diameter", and the ones I use are around .300" or so.
-john
#21
Posted 26 January 2015 - 09:46 AM

#22
Posted 26 January 2015 - 09:55 AM
#23
Posted 26 January 2015 - 11:57 AM
Mr. John,
Did you ever get your "com welding rods"....arc gouging rods?
REDD
#24
Posted 26 January 2015 - 12:04 PM
When/where/how much?

#25
Posted 26 January 2015 - 03:20 PM
Pro motor and car builder
Australian AA/FC quickest car