
Stay-Brite Flux
#1
Posted 27 September 2007 - 06:34 AM
#2
Posted 27 September 2007 - 09:45 AM
The only one I have found is that sold by Slick 7. It is the best-flowing low temp silver solder I have ever used.
#3
Posted 27 September 2007 - 10:29 AM
Anthony 'Tonyp' Przybylowicz
5/28/50-12/20/21
Requiescat in Pace
#4
Posted 27 September 2007 - 10:29 AM
First Place Loser in the JK Products
International D3 Builders Competition
#5
Posted 27 September 2007 - 10:58 AM
I agree, it works much better than a couple of other acid fluxes I've used.
Steve Walker
"It's hard to make things foolproof because fools are so ingenious..."
#6
Posted 27 September 2007 - 11:04 AM
Speaking of torches, I hope to invest in one "someday". My local track has one for sale but I don't know what brands/models are recommended(?). The one they have is priced at $49; is that reasonable? What do you recommend?I also use a torch, the higher heat helps purge out any air bubbles.
Remember, two wrongs don't make a right... but three lefts do! Only you're a block over and a block behind.
#7
Posted 27 September 2007 - 04:55 PM
#8
Posted 27 September 2007 - 08:03 PM
#9
Posted 27 September 2007 - 08:40 PM
Click here for the link to eBay.
Hey, Jimmy, what about this one?Rustle has been using torches far longer than I have but so far a $24.99 Ronson torch has worked for me.

Think it will do the job?

First Place Loser in the JK Products
International D3 Builders Competition
#10
Posted 27 September 2007 - 09:50 PM
I'll try the Stay-Clean flux. I also have an old Radio Schlok oxy-butane torch that I'll try with the little solder wedge trick. I'm only doing HO scale so it's often tight quarters.
#11
Posted 27 September 2007 - 11:45 PM
Stay-Clean is the flux. The bubbling is a good thing, means it is working. Silver solder seems to wet out at about 450 degrees and most 60/40 will wet out at a lower temp. If the joint is smooth, it was enough heat; if it's lumpy or rough-looking, not enough heat.
I used to buy the flux by the case in gallons and repack in small containers for slot use...
I don't think a torch is necessary except for guide tongues but the board guys like them.
Rick Bennardo
"Professional Tinkerer"
scrgeo@comcast.net
R-Geo Products
LIKE my Facebook page for updates, new releases, and sales: Rgeo Slots...
Lead! The easy equalizer...
#12
Posted 28 September 2007 - 05:39 AM

I intend to live forever! So far, so good.


#13
Posted 28 September 2007 - 09:20 AM
That's EXACTLY what I want to use it for; I solder a 1/16" brass guide tongue on top of a 1/16" brass plate.I don't think a torch is necassary except for guide tongues...
Remember, two wrongs don't make a right... but three lefts do! Only you're a block over and a block behind.
#14
Posted 28 September 2007 - 10:02 AM
I have found that if I tin both pieces and use a very hot iron, I can easily solder them together. Mike Steube demonstrated a technique using lots of Stay-Clean flux and an Inland 100 watt iron which worked very well. He actually put solder on the top of the two pieces as well as mating surfaces to get the solder to flow evenly everywhere. After the joint was finished, he just cleaned the excess solder off with sandpaper and Scotchbrite pads.
I would also add that I have done more than a little inadvertent damage to my bench while using a torch. For that reason I have just tried to use the hottest iron available. At this point, that is the Inland unit that I bought at Buena Park Raceway.
If I am having problems getting a good solder joint, it's almost always either not clean enough or not hot enough.
Hope that helps.
#15
Posted 28 September 2007 - 10:11 AM
I'm not much of a "fire" guy. Along with the flame, I'm always a bit afraid of getting things too hot and have them lose their temper. I go with two irons when soldering to 1/16" brass. (BTW, isn't 1/16" for the tongue a bit overkill?)That's EXACTLY what I want to use it for; I solder a 1/16" brass guide tongue on top of a 1/16" brass plate.
Back to flux, for those who will attend the Sano and are flying/can't bring liquids, I'll have some real killer flux at the raceway they can try. I've never had Stay-Clean in the big bottle, but the stuff I have, IMHO, is a bit stronger/better than the Stay-Clean flux you get when you buy the combo with the silver solder. If you get the flux on your skin, it makes your skin tingle to the point that you find yourself walking fast to the faucet to neutralize it.
Mike Swiss
Inventor of the Low CG guide flag 4/20/18
IRRA® Components Committee Chairman
Five-time USRA National Champion (two G7, one G27, two G7 Senior)
Two-time G7 World Champion (1988, 1990), eight G7 main appearances
Eight-time G7 King track single lap world record holder
17B West Ogden Ave., Westmont, IL 60559, (708) 203-8003, mikeswiss86@hotmail.com (also my PayPal address)
Note: Send all USPS packages and mail to: 692 Citadel Drive, Westmont, Illinois 60559
#16
Posted 28 September 2007 - 10:59 AM

I have found that an 80 watt Weller iron, nominally sold for stained glass work, is plenty of heat for soldering even to chassis that are one big slab of brass. Much preferable to torches, in my opinion.
As Jim mentioned, Steube points out in his chassis building video that heat transfers from the iron tip to the work much more effectively if you tin the contact point, even when you are sweating two pieces together. This has been helpful for me.
Our local track owner Steve Foster will place a large piece of metal on a hot plate to warm it up before soldering. It is surprising how much of a difference it makes just warming the piece, even if it's not heated to the melting point of the solder.
Steve Walker
"It's hard to make things foolproof because fools are so ingenious..."
#17
Posted 28 September 2007 - 11:21 AM
Steve, when I was 11 or 12 years old, I had a Weller 100/140 gun that didn't work really well for soldering thick brass.Our local track owner Steve Foster will place a large piece of metal on a hot plate to warm it up before soldering. It is surprising how much of a difference it makes just warming the piece, even if it's not heated to the melting point of the solder.
What I did was place my chassis on the bare concrete floor in the laundry room, douse it with lighter fluid, and light it. After the flames had died down, the brass was preheated enough that the Weller soldered just fine...
I'm real glad my parents never discovered me using that trick!
Uh, Tony, every reference I've seen says not to use acid flux on electrical connections. Is that not a problem for you guys?The Stay-Brite flux works very well... At work we found it to be the best for silver-soldering commutator tabs on our R/C motors.
Gregory Wells
Never forget that first place goes to the racer with the MOST laps, not the racer with the FASTEST lap
#18
Posted 28 September 2007 - 12:15 PM
If you tin both parts and hit it with the torch, you don't have to clean off the excess solder. And the solder get in every little crack and crevasse. Looky here:Mike Steube demonstrated a technique using lots of Stay-Clean flux and an Inland 100 watt iron which worked very well. He actually put solder on the top of the two pieces as well as mating surfaces to get the solder to flow evenly everywhere. After the joint was finished, he just cleaned the excess solder off with sandpaper and Scotchbrite pads.
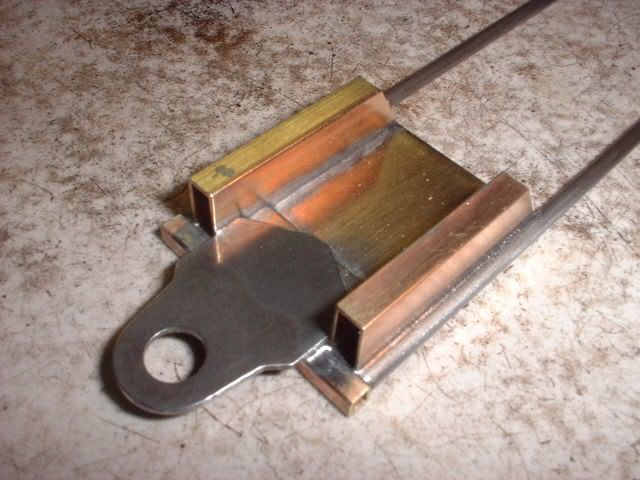
First Place Loser in the JK Products
International D3 Builders Competition
#19
Posted 28 September 2007 - 12:47 PM
We clean them really well. The high temp silver solder we use really won't flow any other way. On multiple winds at the last /first pole it's really important to make sure all the wires make good contact.
Anthony 'Tonyp' Przybylowicz
5/28/50-12/20/21
Requiescat in Pace
#20
Posted 28 September 2007 - 03:49 PM
The phrase, "After the flames had died down..." always get my attention... particularly working at a place where they launch large rockets.

Steve Walker
"It's hard to make things foolproof because fools are so ingenious..."
#21
kkjva
Posted 28 September 2007 - 05:27 PM
I recommend first the Stay-Clean flux, then the Lucky Bob's flux, it comes in a bottle with a brush for applying the flux. As Mike Swiss has said, there are more options out there...
M. Swiss, I'm interested in some of that "skin-tingling" acid flux!
Greg, do that today and you'll be seeing a professional three times a week!Steve, when I was 11 or 12 years old, I had a Weller 100/140 gun that didn't work really well for soldering thick brass.
What I did was place my chassis on the bare concrete floor in the laundry room, douse it with lighter fluid, and light it. After the flames had died down, the brass was preheated enough that the Weller soldered just fine...
I'm real glad my parents never discovered me using that trick!

Be Good,
kkjva