One of the "biggies" is how well you make the comm tab connections. Things like making sure the wire is dead-clean where it crosses over the tabs (or hooks, depending on the type commutator), making sure the tabs themselves are clean and shiny (copper does oxidize, and tarnish) and then getting the actual connection, whether solder on the mild ones (#29/#30/#31) or "welding" (brazing) on the warm stuff.
Afterwards, I think it's also a good idea to clean all those joints from the burned gunk left behind. Anything that might cause corrosion could be a problem down the road. n general, I believe that all the stuff that happens before and after winding are more important than the actual winding.
Here's an arm for a Mabuchi FT16D after welding. Before welding, the poles were "close", within .003-.004 ohms of each other. After welding, everything snapped right to the same resistance readings of .141 ohms per pole. You will also see the last .001 ohms of variance disappear (if the readings are still slightly off) after cutting the comm. Do I hit a homerun every time?... NO! Still, getting itty bitty "fillets" of brazing metal that flows at 1,200F without melting the tabs themselves can be difficult. This is what I shoot for, having them look like nice regular solder joints. These connections are both electrically sound and VERY strong:
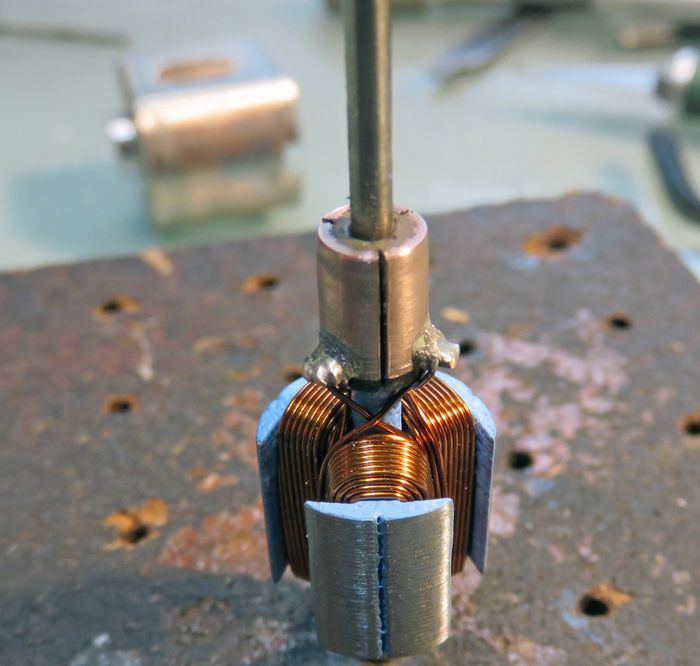
So, just as the great chassis builders here pay attention to all kinds of seemingly "unimportant details", you really have to pay that kind of attention to motors and armatures. It doesn't matter if it's a modern megabuck open or an old Mabuchi/Mura/Champion. For them to be the best they can be performance-wise, it's important that the bazillion little details are taken care of.
-john