Another Mabuchi type I haven't done in a while. These showed-up in a good number of "thingies", and were seen back then as a "better/faster" Mabuchi. While the magnets seem to have been slightly better than your typical FT16D/FT36D, I *think* a good part of the "faster" came from a tighter air-gap and shorter stack. Many of the same problems as with all Mabuchis are still there...as well as the annoying "end bell crack around the bushing" that is now "standard equipment" after decades of aging.
This example was an NOS run-of-the-mill "blue wire" 26D. Gathering parts, I did find a couple of sets of very strong later Mabuchi ceramic magnets. For comparison purposes, the stock magnets measure around 650 or so on my meter. These measure around 1200, which puts them significantly ahead of even Arcos. Like the Arcos, these needed a shim to get the air gap down to "reasonable", so I cut up an Arco shim and epoxied the magnets and shims into the can for a final "hole" of around .590"...about dead-bang perfect for a modern .560" arm (*thirty over works well for most of these old motors). The .560 lams have a much lighter (less steel) profile, so even though the stock Mabuchi lams have plenty of room for winding, there will be less mass to start and stop rotating.
With the 26D being exclusively end bell drive that I know of (*except for custom stuff), I decided to ditch the end bell bearing, even though it was in perfect shape, for an oilite bushing. This particular end bell was perfect and unused, but still had "The Mabuchi Crack"...the slot car motor equivalent of "plumber's butt", so the bearing just fell out. Whether I kept the bearing or not, this would need to be addressed, as I wasn't about to just throw out an otherwise clean end bell dagnabbit. So I drilled two itty bitty holes about 180 degrees apart on the small bushing area, and epoxied the new bushing in with the lo-vis stuff so I could see it seeping out of the holes. That way, the epoxy would bond to the bushing and form two "pins" to key the bushing in place. It also seeped out of the crack a little, which oddly enough I see as a good thing, further "keying" the bushing to the plastic. I also made a collar on the lathe, but decided not to use it because in some applications it might cause difficulty mounting the motor. Besides, I don't think it's at all necessary here, as it all seems solid...certainly WAY more solid than it was and solid-enough.
Having gone this far, I decided to use "bullet-proofing" plates. The post holes just needed to be ovalled-out some for a good fit. I soldered the brush tubes to them for some more insurance. Then I drilled the posts with some more itty-bitty holes, shortened a pair of post sleeves and epoxied them on for another "keyed-to-the-unbondable-plastic" installation.
Having an actual setup to build an arm for, I had at it and did one about the same length as the stock Mabuchi stack minus the fiber end-insulators. More room for winding and the fiber end insulators don't do anything other than help prevent shorts and make for longer coils. Powder coating takes care of the anti-short thing better of course.
Ready for winding!
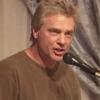
The Mabuchi 26D
#1
Posted 23 November 2017 - 10:21 AM
- slotbaker, Tex, boxerdog and 3 others like this
#2
Posted 23 November 2017 - 10:33 AM
Hi John,
These lams are from Bill Bugenis?
This thing is going to fly...
Thanks,
g
- havlicek likes this
Yes, to be sure, this is it...
#3
Posted 23 November 2017 - 10:42 AM
Hi John,
These lams are from Bill Bugenis?
This thing is going to fly...
Thanks,
g
Hi Geary,
Yes they are from Bill. I don't see doing anything hotter than a #28 wire wind for this motor, and that WILL be very fast indeed! They were done way hotter (*sometimes by me too ), but I think a #28 is as hot as is "reasonable" for the type...right on the edge.
#4
Posted 23 November 2017 - 11:24 AM
Hey John, Happy Thanksgiving.
"With the 26D being exclusively end bell drive that I know of (*except for custom stuff)"
They did make one drive out of both sides. The Classic CM 470.
Don't know how useful it would be to drive out of the can side anyway as most or all 26D brackets I've seen use the EBD side to mount.
- havlicek and MattD like this
Joe Lupo
#5
Posted 23 November 2017 - 11:38 AM
Hi Joe...and Happy Thanksgiving to you too! You're right (*of course!) about "dual-shafted" 26D's like the Classic (*Classic had a seemingly endless variety of motors in general!). I think there may have been one or two others as well. At least I know that Champion had dual-shaft FT36D motors, and I think it was the Champions that had the two holes on the can end, presumably for mounting(?). I have to believe that there were some 26D motors done as can drive (*besides the few I did) back in the day, but have never seen any vintage cars done that way that I can recall???
#6
Posted 23 November 2017 - 06:33 PM
Stock Classic 26-D can end drive
The can is mounted to the motor bracket with self tapping screws thru the holes punched in the can for the magnet stops.
g;
- Jesse Gonzales likes this
Gene Adams AKA Gene/ZR1
ZR1 Corvette owner
Hand-carved balsa bodies, resin body plugs, silicone molds, vacuum bodies
Genes_World@ymail.com
#7
Posted 23 November 2017 - 06:41 PM
Gene, that's most likely a Frankenstein or a CM470 with one shaft end cut off.
Cox made special adapters to mount the 26D in an ISO frame.
That mounting is "creative "
Joe Lupo
#8
Posted 23 November 2017 - 06:57 PM
Gene, that's most likely a Frankenstein or a CM470 with one shaft end cut off.
Cox made special adapters to mount the 26D in an ISO frame.
That mounting is "creative
"
The Cuc as shown has nothing to do with this 26-D as shown.
I made the center brass section do to a hacked attempt by someone in the past trying to mount a 26-D into a 16-D aluminum Cuc center section.
Look here; http://slotblog.net/...mabuchi-ft-26d/,
Classic marketed three types of the Mabuchi FT26 motor. The CM450 was the endbell-side drive type, the CM460 was the can-side drive, and the CM470 had twin shafts.
It is a CLASSIC CM-460, TESTOR MADE A TEMPEST MK-VI
No a cut off armature of a Frankenstein motor
g;
- C. J. Bupgoo likes this
Gene Adams AKA Gene/ZR1
ZR1 Corvette owner
Hand-carved balsa bodies, resin body plugs, silicone molds, vacuum bodies
Genes_World@ymail.com
#10
Posted 23 November 2017 - 09:57 PM
John, I'm curious as to why the endbell mounting screws are so close to the original tabs? And why only 2?
It's weird being the same age as Old People.
#11
Posted 24 November 2017 - 07:46 AM
I've seen Mabuchi motors mounted can drive using sheet metal screws in the magnet stop tab holes. It's certainly not why the holes are there, and always figured it was just a thing people sometimes did. Never knew it was an actual thing that brackets were designed for!
John, I'm curious as to why the endbell mounting screws are so close to the original tabs? And why only 2?
The position of the holes is something I changed a couple of years ago, because when they're lower/further away from the tabs, they can interfere with some chassis. Because of the geometry of a can with two flat sides and two round sides (*as opposed to say an all-round can), two holes offset on the round sides effectively prevent the end bell from rotating. The "shoulder" molded into the end bell that stops it from being installed too-deep into the can also prevent the can from rotating. This became the "standard" method for reinstalling the Mabuchi end bells since the can tabs couldn't be relied on to not break off when re-bent. Even later C can motors that had four factory drilled holes (for either pin tabs or screws) were often used with only two screws (but 4 pin tabs...GAK!), but those motors were mostly can-drive.
***So, two screws offset on the curved sides of the can is plenty strong, prevents the end bell from rotating (*if the can and end bell drilling are done so the end bell is "bottomed-out" on the end of the can) and won't usually interfere with chassis mounting of the motor. It would be a very rare thing (*and unnecessary) to see a Mabuchi drilled for four screws, although I guess (?) someone may have done it. Some Mabuchis came drilled for two screws on the top and bottom flats (Champion), which is fine if done with care, and the bottom screw at least should be countersunk for clearance if it's significantly proud of the can surface. These are usually located dead-center, which would make it easier for the end bell to rotate if not done so the end bell is perfectly bottomed-out on the end of the can.
...anywho (and back on this motor) BAM!, a 44/28 on the .560" stack coming in at .2 ohm:
- Samiam, C. J. Bupgoo, Geary Carrier and 2 others like this
#12
Posted 24 November 2017 - 09:42 AM
There are some motors (*and I know this may sound weird, but it's true) where you know ahead of time they're gonna sing. This one is one of those. The setup all went smoothly, the magnets are stout, the winding went really smooth with no "dagnabbit" moments, epoxying to get full saturation without it running where you don't want it to run and even wind up with just a smidge more near the com than the tail-spacer...was a homerun, the armature had really good natural balance, and the com only took a light cut to get "there". Even before winding, just the assembled arm blank spinning in the setup seemed really nice. While you can still wind up with unexpected fiddling during assembly (*which didn't happen here), or even the unexpected bad surprise, you get a kind of "feeling" about these things.
The motor spins really smooth, fast and powerful. Doesn't get very warm at all and draws just over an amp...bouncing from between .9 and 1.1 amps. Yeah, you can do these way hotter, and people have, but I think this level of power is right in the zone for the 26D...especially if it's expected to live. It's still DEFINITELY a race wind, not your dad's "blue wire 26D" at all. My work here is done!
- C. J. Bupgoo, Geary Carrier and Tom Katsanis like this
#13
Posted 24 November 2017 - 01:06 PM
So the question all this brings up is:
Were there any "factory"-built chassis and brackets made for mounting Mabuchi motors using the holes made by the magnet stop tabs to use as screw-mounting holes?
This is something I've never heard of before, and I have to guess that neither has Joe Lupo. I'm pretty sure that, in the past, Philippe has said that there weren't any stock can-mounting options even for the Champion 26D motor cans that DID have two vertical holes.
#14
Posted 24 November 2017 - 02:58 PM
Sent from my iPhone using Tapatalk
- havlicek likes this
Anthony 'Tonyp' Przybylowicz
5/28/50-12/20/21
Requiescat in Pace
#16
Posted 24 November 2017 - 05:11 PM
So the question all this brings up is:
Were there any "factory"-built chassis and brackets made for mounting Mabuchi motors using the holes made by the magnet stop tabs to use as screw-mounting holes?
This is something I've never heard of before, and I have to guess that neither has Joe Lupo. I'm pretty sure that, in the past, Philippe has said that there weren't any stock can-mounting options even for the Champion 26D motor cans that DID have two vertical holes.
From this very blog by PdL himself:
"One can clearly see the second step on the drop arm, necessary to clear the taller FT26D motor (or "Classic CM460" in slot lingo):
museum-2009-01-14-%20043.JPG
The motor is attached by four self-tapping screws going right through the magnet-retaining holes on the can's end. Pretty crude stuff...
The car sports specific gray sponge rear tires on wide rims. Rims are smooth, no holes, no lip on the tire bead":
maximO
- havlicek likes this
David Ray Siller
MAXImum MOtion
Retired Video Game Creator/Designer/Producer
Thingies are my thingy!
#17
Posted 24 November 2017 - 06:30 PM
Once again, a picture is worth a thousand words!
- Maximo, Gene/ZR1 and havlicek like this
#18
Posted 24 November 2017 - 08:56 PM
Great point, Max.
When I mentioned the brackets I should have said I have not seen aftermarket brackets drive out the can side.
Classic also used the dual drive 26D motor driving out the can side in this funky Gamma Ray setup.
No screws in the actual motor, it is trapped between two chassis pieces.
It cannot be fixed in this application as the motor has to rotate to apply the disc brake.
Joe Lupo
#19
Posted 24 November 2017 - 09:41 PM
Here is a photo of the brass bracket. 2-screws, one at 2 o'clock and 8 o'clock, I did not precisely check the clock locations. The fit up is good.
For what it's worth. it is just a brass axle bracket that directly attaches to a 26-D, Cl.460 can drive with 2 screws. (CSI)
Gene Adams AKA Gene/ZR1
ZR1 Corvette owner
Hand-carved balsa bodies, resin body plugs, silicone molds, vacuum bodies
Genes_World@ymail.com
#20
Posted 25 November 2017 - 07:22 AM
Cool! Even with such a crude (*as Philippe said) attachment, any can drive setup is going to be more solid than an end bell one, so it's neat to see the Classic done that way. Using all four holes would be best of all. Matter of fact, it would make the motor-to-chassis lockup probably the sturdiest part of the whole car, considering that the Classic aluminum stamped chassis would crumple if you looked at it sideways.
#21
Posted 25 November 2017 - 12:40 PM
I don't understand this comment?
Am I crude for posting it or is PdL crude for saying it?
-maXimo
David Ray Siller
MAXImum MOtion
Retired Video Game Creator/Designer/Producer
Thingies are my thingy!
#22
Posted 25 November 2017 - 01:34 PM
Quote: "Even with such a crude (*as Philippe said) attachment..."
I don't understand this comment?
Am I crude for posting it or is PdL crude for saying it?
-maXimo
I'm pretty sure it's merely mentioning how "crude" the mounting is. ie basic/not strong/nothing fancy

#23
Posted 25 November 2017 - 05:07 PM
This mounting is not crude. It was smart.
Someone 50 years ago used their brain and manufactured the competition asp , saved a lot of time, tooling and money by attaching the motor this way. It worked and a ton were sold and people still today keep spending their money for one of these.
Motors have been held in place by one small screw in the end bell by the thousands in the Dynamic motor carriers and others and being even so today,with no complaints or engineering issues.
Other motors are held in place with a brass clip\strap or hold down clips or just solder in place, but everything has an issue.
Question, what is the absolute correct means and method for mounting a motor?, (accuracy: within an angstrom\light-band}.
eccentricity? yes.
O'well going to the dungeon to work on some cars.
thanks;
g;
Gene Adams AKA Gene/ZR1
ZR1 Corvette owner
Hand-carved balsa bodies, resin body plugs, silicone molds, vacuum bodies
Genes_World@ymail.com
#24
Posted 25 November 2017 - 08:39 PM
Quote: "Even with such a crude (*as Philippe said) attachment..."
I don't understand this comment?
Am I crude for posting it or is PdL crude for saying it?
-maXimo
I'm pretty sure the statement is clear. "a crude attachment" refers to neither you nor Philippe, but "the attachment". I can't see how it can be misunderstood.
This mounting is not crude. It was smart.
Someone 50 years ago used their brain and manufactured the competition asp , saved a lot of time, tooling and money by attaching the motorthis way. It worked and a ton were sold and people still today keep spending their money for one of these.
Motors have been held in place by one small screw in the end bell by the thousands in the Dynamic motor carriers and others and being even so today,with no complaints or engineering issues.
Other motors are held in place with a brass clip\strap or hold down clips or just solder in place, but everything has an issue.
Question, what is the absolute correct means and method for mounting a motor?, (accuracy: within an angstrom\light-band}.
eccentricity? yes.
O'well going to the dungeon to work on some cars.
thanks;
g;
Boy, tough crowd here. It almost seems as though mentioning the fact that the attachment method is crude has somehow offended people...but nah...that couldn't be.
By any understanding of the expression, the attachment method is clearly crude. The four holes are not there as a means of securing a motor, and they could easily cause a sheetmetal screw to go in cocked because there's more metal (*the folded-in tab) on one side than the other. I've seen these holes used by "home builders" for obvious reasons...they were there. So it's not like anyone at Classic displayed any great ingenuity using them.
Someone 50 years ago used their brain and manufactured the competition asp , saved a lot of time, tooling and money by attaching the motorthis way.
Well, that's one way of looking at it, but another is that they avoided a really simple solution that wouldn't have involved much if any "time", very little "tooling" and not all that much money. All that was needed was two holes positioned vertically, as Champion did with both 16D and 26D motor cans. Classic could even have just used existing stock and drilled the holes after the fact. They did save some time and money, but they did so by using a crude method of mounting the motor compared to the simpler and way more elegant solution.
Question, what is the absolute correct means and method for mounting a motor?, (accuracy: within an angstrom\light-band}.
eccentricity? yes.
None of this has anything at all to do with NASA-spec perfection. Using these holes certainly worked for them, and using two vertical holes would have worked even better, avoiding the potential problem of the screws being installed crooked. From an engineering standpoint alone, it is a "crude" method, and there's nothing ingenious about it.
O'well going to the dungeon to work on some cars.
thanks;
I'm not getting why the obvious snark is coming my way. Did you design the chassis, because this all seems weirdly like taking personal offense? Otherwise, getting worked up because someone is doing anything other than praise a "lazy man's" method of attaching a toy motor to a model car seems awfully strange for grownups.
I'm going to go work on another 26D...this time a "Classic".
- Horsepower, tonyp, Keith Moister and 1 other like this
#25
Posted 25 November 2017 - 10:38 PM
No snark coming your way, your having a good time with your motors and I enjoy your topics.
Every step in manufacturing cost time and money. Watch the penny’s the dollars will take care of themselves. I don’t think the manufacturer had that large of a profit margins nor did they really care about perfection.
With all the slot cars that were sold were mainly not to well engineered anyhow, to me Cox were well engineered and very scale like.
No, I did not design the original chassis, so why even ask and no I am not getting all worked up.
I don’t agree with the lazy man’s method statement, he saved money and sold the product.
I will agree that they are more better ways to construct slot cars to modern methods, to each his own.
Weirdly, personal offense, awfully strange for grownups, nice ending worded paragraph, really a nice choice of words.
Have a nice time with your Classic 26D project, is it a can drive.?
G
Gene Adams AKA Gene/ZR1
ZR1 Corvette owner
Hand-carved balsa bodies, resin body plugs, silicone molds, vacuum bodies
Genes_World@ymail.com