It made sense we use a JK chassis kit since the IRRA had just started a JK Spec Class geared for non-experts.
With having a request from a customer, Jimmi Bostrom, for a JK RTR chassis, it made sense I take some pictures while building it. The torsion-style pan flex he wanted would be a bit easier to build vs a hinged model. Also, I kept the bends as simple as possible on the six pieces of wire I used.
It was also suggested, if possible, build it without using a jig to help someone who hadn't purchased one yet.
I went ahead and did that. While I used my circa 1984, slate wing car chassis jig, I didn't use the guide post or
any of the scribed markings. I only used it because it's on legs which facilitated clamping.
The finished article is admittedly "Minutia Mania". I did it with the only assumption being, the reader would
know what end of the soldering iron to hold.
I wanted it to have a similar feel as the benchmark series of building articles Lee Gilbert did for Car Model in 1973.
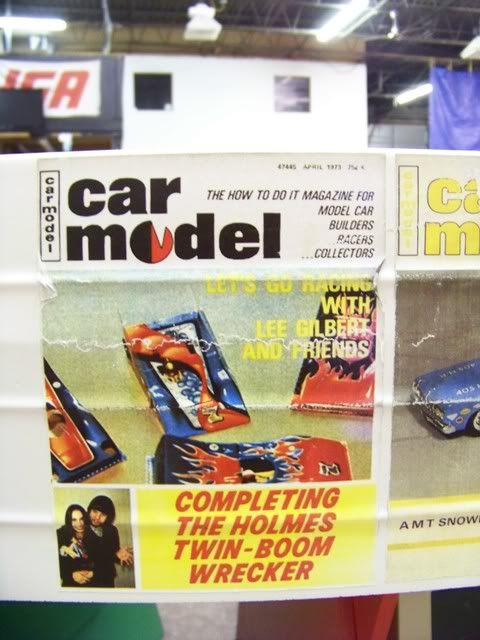
I stopped short of asking my fiancee to clean the chassis while taking a bubble bath, like Lee was able to convince Donna to do.
But hopefully I injected enough levity for the reader to utter at least once, the most heard phrase at Chicagland Raceway's Saturday night races:
"Swiss, there must be something seriously wrong with you."*
*© 2005 - "Sano" Dave Fiedler