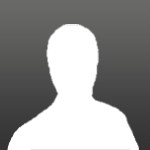
A La Cucaracha build
#51
Posted 23 March 2024 - 10:56 AM
At the moment I only have what Pablo calls "poor man lathe."
I figure I could mount the piece onto a threaded axle securing it with two bolts. So using two Dremels, one where I tightened the axle and the other where I mounted a cutting disc, I could freehand and by eye attempt something that certainly wouldn't be very precise...
Or what about turning a groove IN an O-ring?
How would you do it?
#52
Posted 23 March 2024 - 12:42 PM
With out a lathe I think what you mention will work. If you can clamp the spinning wheel securely and use a hand rest with the cuter you will be better off.
Even though I do have lathes of different sizes I still go to my poor mans lathe for certain sit down operations.
This a cheapy drill press I found in a dumpster at a job site where the contractors had broken the casting while trying to dill something too big I'm sure.
Any way I welded it up and have used for over 25 years. It would hold the wheel solid while resting your Dremel in hand on
the table.
Should be fine
- Fergy, SpeedyNH and Jaeger Team like this
#53
Posted 23 March 2024 - 01:07 PM
That drill press idea is cool, and a good way to use something that would otherwise be trash.
As a kid, I would clamp an electric hand drill to the bench top with a big c-clamp. Then c-clamp a block of wood of the right height to the bench top to use as a tool rest. Then with a tri-angle file ground to the correct point to use as the cutting tool, machine the groove into the wheel. The groove doesn't have to have a rounded profile. A V groove will work just as well. As to the tapered boss, you might be able to find a piece of brass tubing that just fits over the small end of the boss. Drive it on until it is uber tight. Chuck it in the drill chuck, and spin it, tapping on the wheel until it runs true. Then tighten the chuck some more to squeeze the tubing down tighter on the boss.
I don't think I have ever seen anyone put so much time and effort into a cucaracha. Can't wait to see how it runs.
- Jaeger Team likes this
#54
Posted 23 March 2024 - 01:56 PM
I feel the old old school!
#56
Posted 23 March 2024 - 06:25 PM
This is going to be a monster nobody can beat
- Jaeger Team likes this
Paul Wolcott
#57
Posted 23 March 2024 - 07:24 PM
I try harder...
#58
Posted 23 March 2024 - 08:59 PM
Maurizio, you have raised the bar on Cuc improvements. The Cox Iso-Fulcrum was a genius design.
The weight of the motor plants the flag and the front wheels help it instead of being a hindrance.
It's a design that still works well today when done right. By beefing it up and giving it more power you have created a masterpiece.
The power hasn't even come on yet, but you've already won the race
- Jaeger Team likes this
Paul Wolcott
#59
Posted 24 March 2024 - 02:27 AM
In this enclave of passionate baby boomers that is slotblog.net, we all pursue a ridiculous and anachronistic ideal: improvement.
#60
Posted 24 March 2024 - 05:41 AM
That guide tongue looks plenty strong. You could also insert a piece of piano wire in the guide post & into the guide blade for some extra strength.
You could also insert a piece of piano wire in the guide post and into the guide blade for some extra strength.
Or use one of Mike Swiss' upgraded guide flags with post and blade modifications...
Not really in the center!
- Eddie Fleming likes this
#61
Posted 24 March 2024 - 06:46 AM
Here is my Cucaracha just at the end of Cuca Day 2024. A 14th place out of 24... not very good...
You can see the rear reinforcements on the chassis. For the rest just some weights and the block with aluminum sticker of the swing arm.
Two ball bearings at the front.
The engine is a rewound 16D from "Schiatt."
This is instead the swing arm modified in the same way as what was done in the '60s, with the rear joint to guarantee the distribution of power. It is designed for mounting a 26D.
- SpeedyNH and Jaeger Team like this
#62
Posted 24 March 2024 - 07:36 AM
Is the rear joint like a Pizzi joint, letting the motor pivot?
Don
#63
Posted 24 March 2024 - 08:51 AM
#66
Posted 25 March 2024 - 04:29 PM
When designing a slot car, the simplest things have always been successful. Therefore I am afraid that all that get busy and fuss around a guide could turn out to be an own goal.
Anyway, here are all the pieces before cleaning, tinning, mounting and soldering in place...

#70
Posted 26 March 2024 - 07:32 AM
If it hits anything it's probably going to hurt something. And it probably won't be your Cuc
- Jaeger Team likes this
Paul Wolcott
#73
Posted 27 March 2024 - 04:10 AM
For those who do not remember or have not lived the times of Cucaracha, here I compare the stansard front wheels and those that I recovered after being in the drawer for many years.
Notice how the original (in early series) the ball bearing was trapped by a rivet in the aluminium. This rivet was filed down until the bearing was freed so that it could be used for the rear axles. At that time, especially in Italy, you couldn't find such small bearings with measurements in inches, now it is easy to insert and epoxy a modern (and cheap) bearing into the old rim.
- Pablo likes this
#74
Posted 27 March 2024 - 07:53 AM
Those wheels have 18 BB's. (I counted them)
- Jaeger Team likes this
Paul Wolcott
#75
Posted 27 March 2024 - 12:01 PM
18 balls, with a separator?
I intend to live forever! So far, so good.

