With a little more knowledge about these drag motors (a dangerous thing), I set about to winding an arm for the setup I'm building. The stack was assembled from some .014" lams of unknown origin with a thicker leg. On this one, in addition to the usual breaking of all the sharp edges at the stack ends with a tiny diamond point, I coated the stack with the same HT epoxy ("Duralco 4461") as I use for coating the coils. It's much tougher than the furnace cement and more closely approximates the coatings on commercial arms...although it's a relative pain in the keister to do it this way. Once again, it got a Bugenis com and I'm much more comfortable welding these things now
(with some very helpful thoughts about that from Bill). The wind is 25T/#25awg and that's the wind that Don Weaver had asked about originally. Because the crown is somewhat thinner on these lams, I was able to work out a nice tight pattern to get that much big wire on there with no problems. I'm always throwing out wire when I have to figure this stuff out, but I have a few different types of winds I can go through now
(after a lot of sore fingers) to see how to approach these things. That's one of the things about lots and lots of practice that comes up. If you get stuck winding one way (there are a bunch of ways to do this), you may never find a good method for a getting a given wind on a particular blank. It can pay to think outside the box here. Anyway, here's what I got:
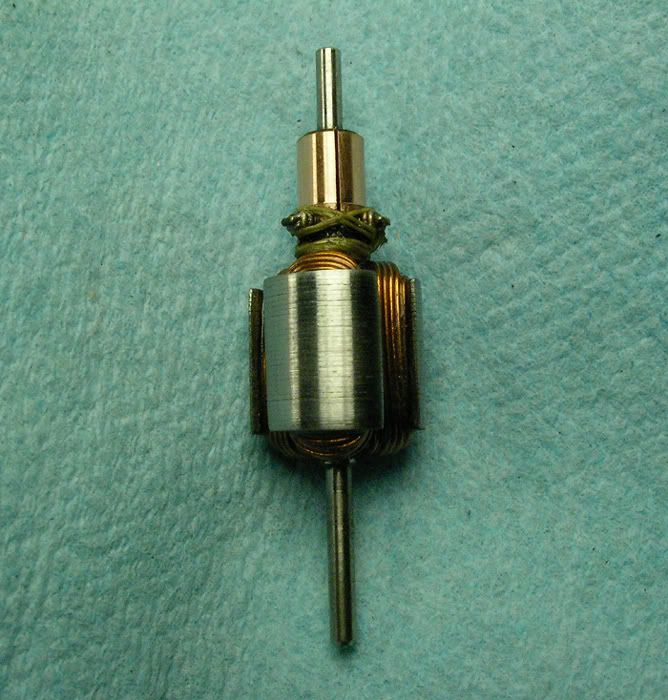
This one I'm going to send to Bill for dynamic balancing and we'll see what's what when it gets back. It was spaced and setup for the test "drag" setup and is a nice fit. It's got way more wire on it than I would have considered putting on there normally...but ???
-john