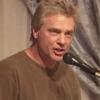
#3176
Posted 27 September 2011 - 11:10 AM
Barney Poynor
12/26/51-1/31/22
Requiescat in Pace
#3177
Posted 27 September 2011 - 11:23 AM
The meter you have is now sold as a BK Precision 1095B. Maybe they can do a repair.
I am off to the ISRA Worlds in Brazil this evening with a bunch of untested (due to the flood) Havlicec wound eurosport motors.
Bill
#3178
Posted 27 September 2011 - 02:14 PM
Yeah, it's almost funny because for the first couple of years I started winding again, I was fine using a regular multimeter thinkiung it wasn't THAT important. Now I feel like I'm working blind after having gotten used to being able to "really" test the arms

-john
#3179
Posted 27 September 2011 - 04:48 PM

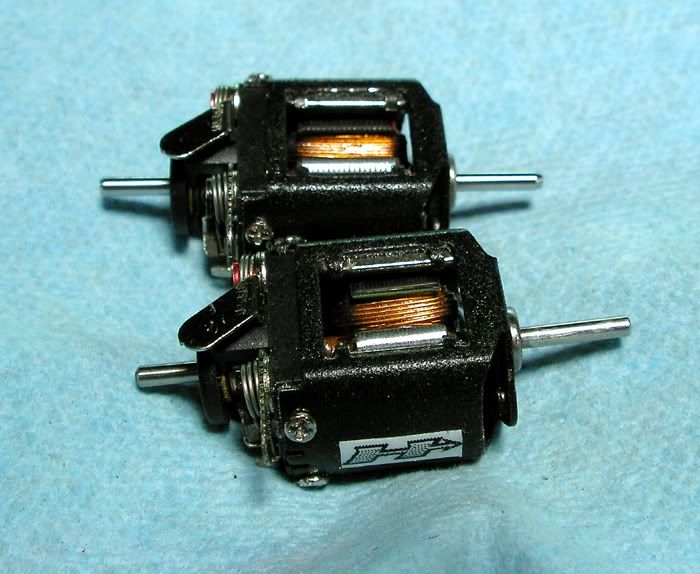
-john
#3180
Posted 27 September 2011 - 10:34 PM

All three timings produced the same trace!! Same peak RPM, same torque, same rates of accelleration...the difference was only this. The high timed arms drew more current and ran hotter. 10 amps on the dyno at peak rpm for the 22* arm and 17 amps for the 30* arm under the same conditions. The lower the timing the cooler she ran. In ceramic motors

Oddly the 22* arm has been the quickest in the car but by less than normal data scatter.
Point is..timing is key to these beast. Keep it lowwwwwww. I know, road race is different, motors run longer and it's more of a problem but the direction isn't going to change. I know of at least one fella working with 10-12* timing in some pretty silly winds with good results.
So hard a judge they hope never to meet as themselves.
#3181
Posted 28 September 2011 - 02:02 AM
I would think for Drag motors, you would want a middle of the road timing, something that will have both good grunt and yet still enough timing to have a decent top end. Although a lot of drag cars have ridiculous gear ratios in them!
#3182
Posted 28 September 2011 - 05:33 AM
-john
#3183
Posted 28 September 2011 - 08:01 AM
I would think for Drag motors, you would want a middle of the road timing, something that will have both good grunt and yet still enough timing to have a decent top end. Although a lot of drag cars have ridiculous gear ratios in them!
10* eh? Pretty punchy I would think? Yea, that's a question.
Now that is interesting. My Neo/FC which has been 139.15 MPH on tall gearing has run .443 @ 126.26 MPH with a short time of .0605 seconds on shorter gearing with a motor build of .490 hole, KRM Quad Neo that gauss 3800. .480 Koford L blank 64 wind at 15* timing. Low and very tight. I have other motors that are in the hunt with gaps around .020 at 24* and that about brackets my range.
John, you are correct on the stock black Hawk Neo's. Poorly matched indeed and as a composite Neo about as strong as a set of Parma ceramics. I meter the stock Hawk ceramics around 900. 25* has been about the top for both sets in my testing.
So hard a judge they hope never to meet as themselves.
#3184
Posted 28 September 2011 - 12:05 PM
Regarding neo magnets, have you tried Pro Slot's new Velociraptor magnets? While the name is dreadful, I'm told the magnets are excellent and were specially made to Dan De Bella's specs. I think that the Hawk neo magnets are linear, while the Velociraptor are radially orientated.
Personally, I prefer polymer cobalt magnets for Euro-type motors -- if I can find them - and never more than 15* advance.
With kind regards,
Russell
Russell Sheldon
Cape Town, South Africa
--------------------------------------
#3185
Posted 28 September 2011 - 01:23 PM
My "BlackHawk" motors look incredibly awesome! The wrinkle finish looks so purposeful too!
Regarding neo magnets, have you tried Pro Slot's new Velociraptor magnets?
Hi Russell,
The Velociraptor Neo-magnets are what I sent John to replace the stock mags in my BlackHawk motors - it should be very interesting to see how they run. I'm looking forward to testing them out!
Ernie
#3186
Posted 28 September 2011 - 02:22 PM
Regarding neo magnets, have you tried Pro Slot's new Velociraptor magnets? While the name is dreadful, I'm told the magnets are excellent and were specially made to Dan De Bella's specs. I think that the Hawk neo magnets are linear, while the Velociraptor are radially orientated.
Hi Russel, and many thanks


Personally, I prefer polymer cobalt magnets for Euro-type motors -- if I can find them - and never more than 15* advance.
I've yet to build any motor with cobalt magnets and all the eurosports arms I've done went into some pretty hairy setups built by Lou Pirro, and wound to Bill Buegenis' specs. I've never held a functioning strap motor in my hands working down in the salt mines at the winding crank

Hi John,
My "BlackHawk" motors look incredibly awesome! The wrinkle finish looks so purposeful too!
Hi Ernie and thanks

_______________________________________________________________________________________________________________
While working on Ernie's motors, I did some experimenting with brazing as I had to braze the tabs on the stock Hawk com for one of the motors and they're kind of fragile. I came upon an improved method of brazing that seemed to worked more reliably/consistently. Having just finished another Hawk rewind (with another Bugenis com), I tried the same method and it really does improve things significantly as far as electrical integrity and mechanical strength, putting what looks almost like a neat little fillet of solder (*but it's actually 1200°F jeweler's silver) on the tab. Things are still a tad touchy for me when doing this...especially if I don't time my foot on the switch and contact with the heater tip and the tab, resulting in an arc and often a demo'd com tab. In any case, here's a closeup of some of the brazed connections with that nice little lump of silver on there:
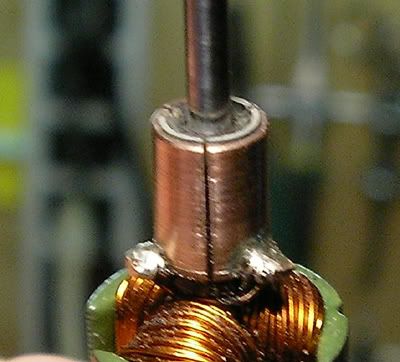





Speaking of the above Hawk, I took the neos out of one of the new Hawks and replaced them with a set of ceramics that measure nicely at around 900 or so. That's the setup for the above wind which is a #28. The arm comes in at almost precisely .195 ohms per pole (my meter sometimes works when the mood strikes it

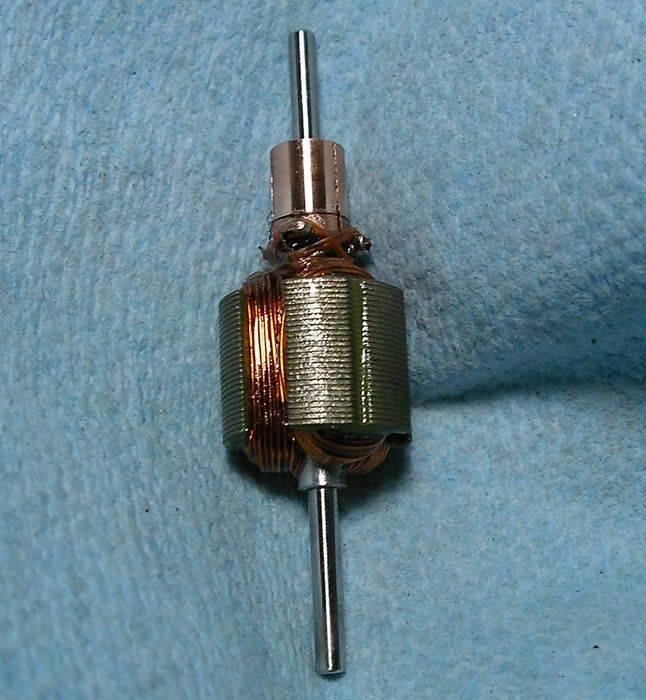
I'm pretty sure that this arm in the Hawk setup with the ceramics will be a screamer, that's also not so "on the edge" as it would be with the neos...but I probably will test it with both magnet types to see what's what.
Last thing, Bill is in Brazil for the Eurosports Worlds. Does anyone know of a good dynamic balancing service that takes PayPal? I have a little bit of money in there I'd like to burn up and this arm seems to deserve the "full monty". TIA
-john
#3187
Posted 28 September 2011 - 02:49 PM

I intend to live forever! So far, so good.


#3188
Posted 28 September 2011 - 03:28 PM
BTW no one has a method yet to produce radial Neo magnets. You can segment them to mimick it though. Sort of

So hard a judge they hope never to meet as themselves.
#3189
Posted 28 September 2011 - 05:42 PM
Those micro-welds look so precise as though it was machine welded!! Do you use a micro-tip to do this?
It's always exciting to take one's skill to a higher level. Your technique is awesome John!
Many thanks for taking the time to put these "BlackHawk" motors together for me.
Ernie
#3190
Posted 28 September 2011 - 05:46 PM
The stock com seems pretty skinny for such large brushes (I think Mike Swiss did a neat brush mod to overcome this) and after seating/breaking them in, they look to me like they would basically almost always be shorting between two com segments.
It sounds like it is not a good thing John! Shall I expect a "short" track life - LOL (pardon the pun!)??
Thanks!
Ernie
#3191
Posted 28 September 2011 - 06:38 PM

They're really not properly called "welds" since there is another metal used to fuse the wire to the tabs. I think in slots though that all these connections are called "welds" generically. The connections at the com are really important though because you can see the change in the resistance of each pole as you "weld" them. On this particular arm, the poles' resistance was off by maybe a couple of hundredths of an ohm before the welds. Afterwards, they were within a thousandth of an ohm or so. Then I cut the com and they were off again by a little

It sounds like it is not a good thing John! Shall I expect a "short" track life - LOL (pardon the pun!)??
Beats me


-john
#3192
Posted 28 September 2011 - 06:50 PM
Would "solder joints" be the better definition of the "welds"?
Thank you John!
Ernie
#3193
Posted 28 September 2011 - 06:59 PM
Would "solder joints" be the better definition of the "welds"?
Nope, "solder" is a name for a bunch of low-melting point alloys with tin and sometimes lead or silver or other small trace amounts of metals. These connections are (I think) more properly called "brazed" connections.
-john
#3194
Posted 28 September 2011 - 07:05 PM
Thanks John!
Ernie
#3195
Posted 29 September 2011 - 05:47 AM
When I'm not really focusing on the method used, I'll say "welded" myself as a generic term. In this case, I just wanted to be clear since looking at the picture, it looks like solder (to me anyway). Really, when you think about welding, it's generally fusing two pieces of metal with heat. "Soldering" is bonding two pieces of metal with a third metal which is solder, BUT in this case the third metal is silver...so it's like "high-temperature soldering". Since solder alloys melt at anywhere from say 375°F to 450°F, and the silver I use melts at around 1200°F, there's a big difference as far as the strength of the joint and it would be impossible for the heat of the motor to throw a com connection IF the brazing is good. Like I said above too, silver is one of the best conductors...if not THE best (I think it's even better than gold in this regard), so the silver adds no significant resistance to the equation. With copper melting at just under 2,000°F, the silver can fuse at safely below the melting point of the copper, but waaaaaaaaaaay above any likely temperatures the motor would encounter without vaporizing first

As a side thing, I take apart many motors where the com connections ARE "welded" and it looks to me like they use some sort of resistance spot-welding type process. Probably a very short/very hot "blip" to fuse the tab and the magnet wire. I don't know which is the preferred method for high-end motors or if both are used, but it would seem to me that brazing might be the better way...although less practical for higher run production arms. The thing is, it can be difficult (at least at the home brew level) to do brazing on such a small thing as a com tab and in many cases with thin magnet wire and get good results. I've been refining this one detail for a few years now, and am still improving. Even the shape of the heater tip is REALLY important, as is the material the tip is made from and the power source. The brazing metal also comes in many types and alloys, so there's a bunch of experimenting to go through with that. Now I have a way to do this that leaves a better fillet of brazing silver on the tab, and it's only because I had to figure out a way to do one of your Hawk motors...so thanks!

-john
#3196
Posted 29 September 2011 - 01:42 PM
it's only because I had to figure out a way to do one of your Hawk motors...so thanks!
Allright - I'll take responsibility - LOL!!!
Seriously John, I must thank you for your time and effort that you put into each and every "rewind" build you produce. Especially mine!!
I am indeed grateful!
Ernie
#3197
Posted 04 October 2011 - 06:24 PM

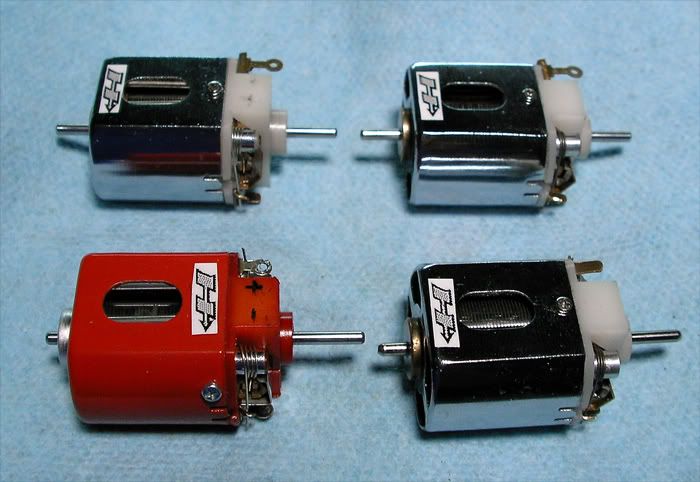
-john
- MarcusPHagen likes this
#3198
Posted 04 October 2011 - 11:33 PM
What a set of "gems". That red on red motor looks hot. It's exciting to see your work go "international" - congratulations.
Ernie
#3199
Posted 05 October 2011 - 05:09 AM
Over the past couple of years, I've sent quite a few motors to various countries in Europe...a bunch to Germany, England, Italy and even a couple to France and Spain. They seem to like the vintage stuff a lot over there, as well as thingies too...my kinda people!
-john
#3200
Posted 05 October 2011 - 07:58 AM
The commercial slot racing boom was short but intense here, and a lot of my slot buddies experienced that at the time (66-68), some then stopping and some continuing through the club scene in the 70s and 90s. Fortunately, there are also some younger racers who like the vintage scene for various reasons - maybe it reminds them of racing with their grandfathers...
I'll be back on the thread pretty soon, because at our last vintage meeting I managed to burn out two stock Russkit 23s! One I lent to a friend when his own period rewind burned up during qualifying (the Russkit ran well, but popped a wire after three segments), and the other in my own Russkit Porsche Super Spyder, which made it through the 8 heats, but started seriously slowing down in the last segment and a half. Haven't looked at that yet, but just disassembled the loaner last night and the windings on one of the poles was darkened, and a wire had come off the commutator...
Will be rewinding that one and checking out the other... I counted about 107 to 109 turns on the Russkit 23, and the wire may be 32, 33 or 34, can't tell for sure! (I thought I had seen Rocky identify these as 34, but that seems kind of small for a "6V" motor.)
My poor friend also loaned an MPC Mako Shark to another friend, and that motor burned out too! Very unusual to see three usually solid motors burn out. It's an electronic power supply, rated at 120 amps (they also run X12 motors, it's the Nieuport club in Belgium); not sure what the voltage was set at, but maybe higher than 12 volts. And besides us, didn't seem to be an unusual number of motors getting burned out - it was my first in all these years of vintge racing!
To be continued...
Don