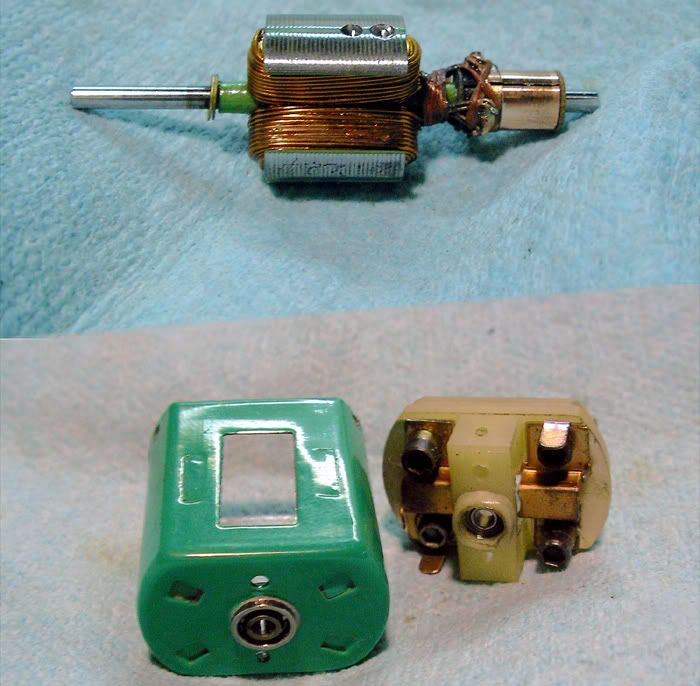
-john
Posted 28 May 2012 - 04:08 PM
Posted 28 May 2012 - 04:19 PM
Paul Wolcott
Posted 28 May 2012 - 04:26 PM
Posted 28 May 2012 - 04:44 PM
Paul Wolcott
Posted 28 May 2012 - 05:46 PM
Posted 28 May 2012 - 05:53 PM
Posted 05 June 2012 - 09:39 PM
Posted 06 June 2012 - 06:19 AM
Posted 16 June 2012 - 01:03 PM
Posted 16 June 2012 - 03:09 PM
Posted 16 June 2012 - 07:08 PM
Posted 17 June 2012 - 07:48 AM
Posted 17 June 2012 - 09:34 AM
Posted 17 June 2012 - 10:16 AM
Posted 17 June 2012 - 02:06 PM
Posted 17 June 2012 - 03:25 PM
Posted 07 July 2012 - 11:28 AM
Posted 07 July 2012 - 03:30 PM
Posted 08 July 2012 - 08:16 AM
John, this is a great idea. Most slot racers have access to a handful of these motors & arms. A few questions, if I may ask. Did you use drill blank shafts on these arms or something else? Are you using .078" piano wire shafts on anything these days? What gage(s) of wire did you wind on these short stack arms? Were they relatively mild winds? How do these arms compare to those in the SCX(?) motors you used to build?
Are you using .078" piano wire shafts on anything these days?
What gage(s) of wire did you wind on these short stack arms?
Were they relatively mild winds?
How do these arms compare to those in the SCX(?) motors you used to build?
Posted 08 July 2012 - 05:39 PM
Posted 19 November 2012 - 11:24 PM
dupont that makes the highest temp epoxy told me that since epoxy is organic there is a temp limitation and that limit seems to be around 600f(jim greenaway used this single component which looks to be the same as the cotronics product,since the highest temp coated magnet wire is mws ml coated 240 C temp wire since the epoxy exceeds this temp its better than you will need since the wire coating will fail before the epoxy.There is a ceramic 1200 F temp coated but costs about $500.per pound not worth it,dont believe koford when he says he uses 800 f epoxy it doesnt exist,the dupont research scientists told me recently and explained that the limitation of epoxy polymers is around that 600 F unless you add other materials to it which renders it unfit to flow into the fine spaces of the windings.I was actually hoping you had some of that secret good stuff! lol
I'm still hoping to find something that will hold up to 800 degrees or more, but i just havent been able to find anything of the sort.
If you find something, definetlly let me know, I'd love to get my hands on some!
Posted 02 December 2012 - 09:23 AM
Any epoxy good to even a little over say 400F should be fine for about anything anyway. Magnet wire insulation (also being an organic compound) is only good to that range or less and then things like end bells and magnets would have failed anyway. Heck, if the can on a motor ever got to 400F, the body would probably melt around the motor just from being close to it. There's also sometimes a problem properly mixing epoxy in the very small quantities necessary for encapsulating the coils on a single armature. I've had arms "foam" when I hadn't been as careful as I should have been (over-catalyzed), and I've had arms fail to fully cure (under-catalyzed) too. There are single part (and also two-part) epoxies that are better suited to motor coil encapsulating from a "bomb-proof" standpoint than the stuff I use, but they have cure-schedules that make them difficult in a home environment. Really, even on the top open type motors, bomb-proofing is just as much about very accurate balancing and stuff like com-capping and the accuracy/precision of the motor setup as it is the epoxy. Over-the-top claims about epoxy temperature ratings are probably just good ad-copy.
-john
Posted 21 December 2012 - 01:36 PM
Hey John I just received the arms real sano work and that skewed arm is wild looking i cant even imagine how you could even wind it,and eventhough the double 26 is so difficult to wind because theres not enough room for the amount of wire, you ve made it look like its not overloaded,thanks again,your a cool dude in a loose mood(to quote out dated jargon), Who do you recommend for balancing.Hey i miss the island my sister lives in port jeff and i miss the blue fishing on the sound and stripers at the montauk lighthouse.
Posted 31 December 2012 - 08:03 PM
Hi Bruce,
Glad they got there safely. There are lots of places to get the balancing done, and of course ProSlot does this (among many other motor services). Bill Bugenis does balancing and he can be contacted by PM here. Proformance (PRI) also does balancing and other motor services. Many use Alpha as well for balancing and various motor services. Fast Ones (Ron Hershman), Koford and others offer various services as well. Often these kinds of services can be ordered through your local raceway as well...so there's a possible way to go besides direct.
-john
Posted 14 January 2013 - 12:00 PM
The only thing I might possibly add would be a turned down Mura or Ploslot endbell on a Falcon 7 can to put the arms in.
I have a shortened Falcon and a new arm from another F7 that thew arm was bad in. The arm is in pristine condition and the insulation looks very nice!
I have also a PS -4002 endbell that basically is a press on fit on the F7 can without any cutting in it, but I have seen in some posts here that very often a cut down mura C-can endbell is recommended? Isn't the PS endbell good enough? Is surely is less work with that one!
Regards,