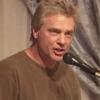
#2126
Posted 19 November 2010 - 08:53 PM
-john
#2127
Posted 19 November 2010 - 08:59 PM
THAT'S ONE BAD MAMA JAMA !!! So what have you got in mind for it?? Inquiring minds need to know

Good thing I sent those motors off to you today, because the way your tearing into these things, your gonna need them

Vic
#2128
Posted 19 November 2010 - 10:20 PM
#2129
Posted 19 November 2010 - 10:38 PM
As always great work, i to am interested to see what goes in there, i agree Kim John has been there for a while now.
#2130
Posted 20 November 2010 - 07:15 AM
Kim, the one-piece cans like the mini motors and whatever this was (maybe a small RC motor?) can be done this way because, after cutting the top and bottom, there's still something left to carry the bushing. We'll see if this thing works...I sure hope so because there's a fair amount of work in it already. These things are kind of fragile after cutting, although screwing the endbell on does tighten them up significantly. Best would be bracing the can to the rear axle carrier using either a piece of piano wire soldered directly or a hinge tube to a wire brace so the motor could be removed easily. For casual running, it's probably OK as is...but the real question is whether it will work well enough to have justified all the effort. A can like this machined out of a solid billet could be made to be both way more accurate as well as strong, without sacrificing too much in the weight department. After all, this thing barely weighs anything at all as it is.
-john
#2131
Posted 20 November 2010 - 10:11 AM


Oh wait I know,,, you could tell us, but then you'd have to kill us right?

What ever you choose to install, I'm sure that little thing is gonna scream !!!
Vic
#2132
Posted 20 November 2010 - 08:53 PM
That looks like it's gonna be a mighty "baaad" motor!!! Is this your version of a "wing car" motor? it kinda reminds me of one. Is it about the same size also?
Very nice work as usually. I really like the "buss bars" - is this the correct terminology for the "positive/negative" blade connectors protruding from the end bell please?
Thanks for granting my request John. I want one now - pleassssseeee - LOL!!!!
Ernie
#2133
Posted 21 November 2010 - 09:17 AM
I have no clue how well this motor will do, but can't see it being a total dog...maybe just a partial dog


-john
#2134
Posted 21 November 2010 - 09:56 AM
http://www.lslots.co...worlds2010.html
Chassis are scratchbuilt: Send a CAD drawing and some pieces of Swedish or German Cutlery steel to an EDM house and back comes a eurosport chassis kit. Solder it together and there you go.
The EDM machine can cut anything in 2 dimensions you can draw.
Bill
#2135
Posted 21 November 2010 - 01:09 PM

-john
#2136
Posted 21 November 2010 - 01:36 PM
Bill
#2137
Posted 21 November 2010 - 03:51 PM

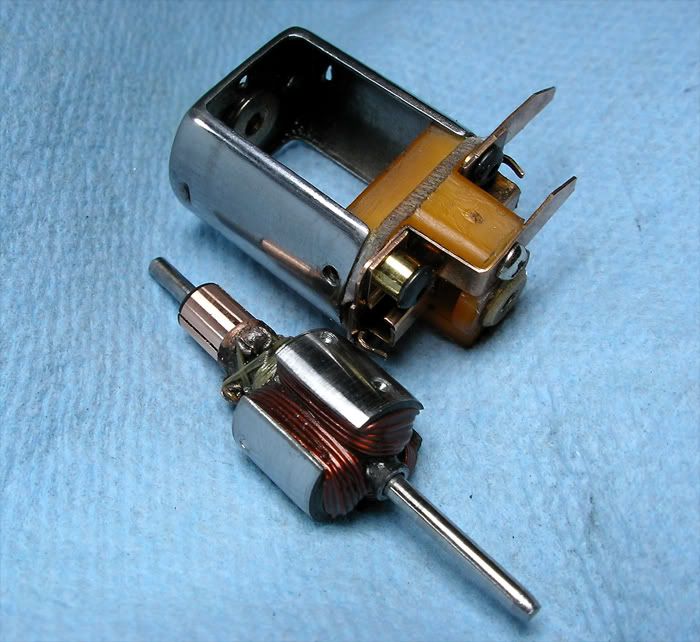
With the bits I've been able to pick up here and there doing all these arms, even the thick web Muras are getting a little easier and more consistent.
-john (ready to wind a bunch more of those 25's)
#2138
Posted 21 November 2010 - 04:25 PM
wow that motor is awsome i love everything about it, the arm looks like it's chrome plated as does the can, itshould really have some power it looks fast just sitting there.
#2139
Posted 21 November 2010 - 04:31 PM



-john
#2140
Posted 21 November 2010 - 05:05 PM


Vic
#2141
Posted 21 November 2010 - 08:31 PM
-john
#2142
Posted 21 November 2010 - 09:03 PM
Yes that is a very pretty motor let us know how it runs.
Ok it's time for a new build, first pic below shows an old Mura group 15 it does look a bit on the sad side but i think it's a good candidate for a hi po rebuild i would like to see just how much power i can get out of this motor without welding the comm tabs because i have no way of doing that, second pic shows the motor torn down and i opened up the cooling holes last pic show the arm i am going to use it's an old Koford group 15 it should work as the shaft is straight and it has a good comm. I am going to try 24 gauge wind as the magnets look to be pretty strong and they pull pretty hard without the brushes, with any luck it will stay together but i have my douts wish me luck.

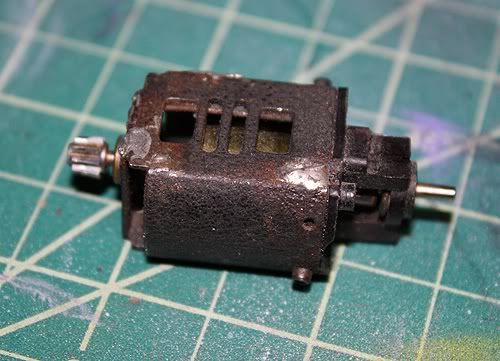
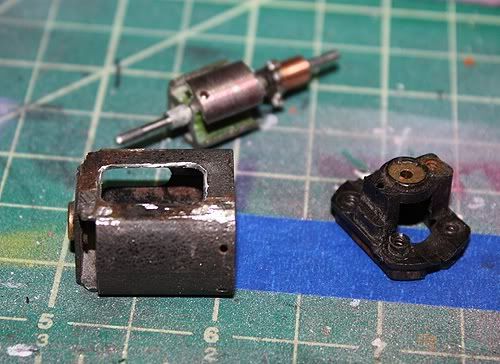
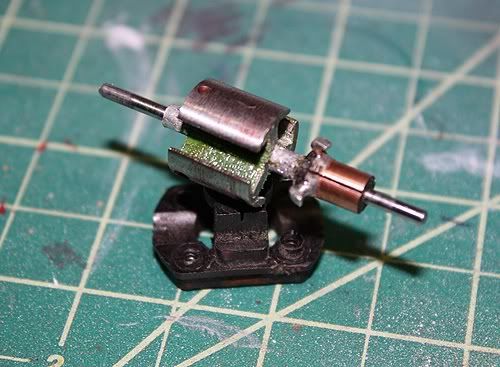
#2143
Posted 21 November 2010 - 09:28 PM
That's a nice Mura/Koford platform to build on and it helps to start with quality materials. Be mindful that the arm was already balanced and that can either work for or against you. The blank has plenty of room inside to wind and the com looks hardly worn at all. Since you're not going to braze the com connections, it's a good idea to get the inside of the tabs clean to get room in there and then try and crimp them over the wire before soldering. The mechanical connection of the crimp can help keep things together some. I've done a lot of this type thing along the way and these things make really cool projects. They can be run for a lap or so with soldered connections, but a 24 is serious medicine. Do you have a wind in mind for the "big wire"?
-john
#2144
Posted 21 November 2010 - 11:16 PM
I am going to do what you said and clean the comm tabs before i start winding it's a good idea, i am not shore how many turns of 24 gauge i should use because i have never tried a wind this hot if you have any thoughts on it i am all ears. I am hoping it holds together with the solder, crimping and a few coats of epoxy either way it should have some power at least for a short time.
#2145
Posted 22 November 2010 - 01:52 AM
Very nice arm - as usual!
Just curious - if you have an arm that has been previously balanced with no spare stacks available to replace the drilled stacks, would it be possible to use epoxy to fill in the drilled balance marks, "blocksand" the epoxy flush and rebalance the arm?
Robert,
I'm looking forward to seeing your rewind!!
Thank you.
Ernie
#2146
Posted 22 November 2010 - 06:32 AM
Filling the holes won't work, first...it might let go and second the weight of the epoxy isn't nearly what the weight of the steel removed was so it's not worth it. I guess some solder might work but it weighs more than steel so it would likely cause errors in the other direction. Besides, to get a good solder bond, it's probably necessary to use acid and that might get between the laminations and cause a mess down the road.
Robert,
If you use a single continuous piece of wire when winding, you might want to plan what pole you start on accordingly. Oftentimes, the last pole can be slightly heavier than the other two, and the last com tab slightly heavier because of the two ends of magnet wire overlapping...depending on how you attach the wire at the tabs. You can also see what the balance condition is like without any wire on the arm and plan your winding sequence accordingly. It can help to mark the poles with a Sharpie ..."A< B< C or 1>2>3 " from heaviest to lightest or whatever code you want before winding. I've done some that were already balanced like yours and had them turn out OK with some balancing touch-up afterwards. If the arm is more than a little out after winding, it may be impossible to remove enough metal without weakening the arm because of it having been drilled already.
With #24 wire, you're going to be down in the 19-20 turns range with that arm and setup...even less believe it or not. When you're doing so few turns of such massive wire, neatness really counts. Think about it, if you're doing 80T/#30 on a FT36D, you can be off by as much as a couple of turns from pole to pole and it's a small change percentage-wise. It's not good, but it's not a deal breaker and you'd be surprised to find out how many factory arms are off, and that's not even looking the length of wire per pole. When you're doing only 19 turns, being off by length of only 1/2" (about a half turn) is way more significant. Try and match your winding patterns from pole to pole as well as the number of turns. Count how many turns are on the first layer before you "turn around and head back towards the com...the second layer etc. and also try to duplicate the way you make the turnarounds as you start on the next layer...which side of the pole you overlap the wire on and how you handle the pole ends when winding them. This project can be a GREAT help for future winds because seeing what's going on is easier with heavy wire...but actually winding is much more difficult. It's a little like training for track with ankle weights and then taking them off for the event

Plan on throwing away wire so you can work on patterns and technique. It's better to waste some wire than to have an arm all done and it not being what you planned.
Have fun!
-john
#2147
Posted 22 November 2010 - 08:18 AM
I agree John even a small error with this large guage wire might cause a problem, i will mark the stacks to keep track of the heavy one and try not to start and end my wind on it, i think i will do a few winds on this arm for parctice first before i solder and try to keep track of my winding pattern before i commit to the final wind. Thanks for your help.
Hi Ernie
I hope it goes well we will see, i will post pics either way.
#2148
Posted 22 November 2010 - 09:26 PM
I, too, have a number of rusty Mura hulks (almost identical to what you've started here) that I want to return to pristine condition. As a matter of fact some of mine are in WORSE shape than yours. But I can see the potential beyond all the rust, so I know I can save them. I probably won't do any #24's (well maybe one) but most of mine will be #25's - #28's and maybe some doubles. I'm hoping to return to motor building next year and maybe even open Motor Shop up again. Gee, I'm only 101 pages behind John"s "Arm Winding" thread. Do you think I'll be able to catch up?....yeah, I don't think so either. Carry on Robert and John. You guys have some good things going on here.
"We offer prompt service... no matter how long it takes!"
"We're not happy unless you're not happy"
"You want it when?"
#2149
Posted 22 November 2010 - 10:19 PM
Thanks Doug for making mention of me in there with John but i am not even close to the level he is at as i am just starting the real high performance winds and have a lot to learn. I think you should get back into motor building and don't worry about catching up with any body just go at your own pace and a have a good time building, i like those old Mura motors they have good cans decent magnets and pretty good brush gear but they are a bit heavy, i am going to guess that this motor was made around the late 1980's to early 1990's.
#2150
Posted 22 November 2010 - 10:30 PM
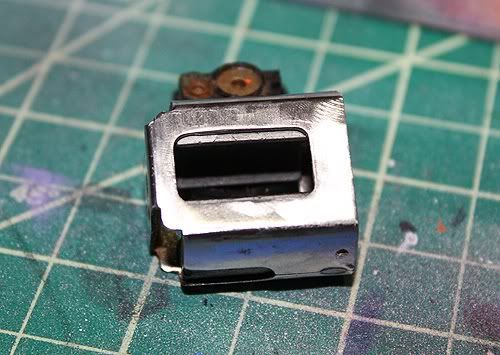