Okey dokey, time to finish up the 26D step-by-step motor.
Back on the arm, it just needs some balance work. While dynamic balancing is the best and most accurate way to have at this, you CAN do fine work with a set of razor blades and a solid balance block such as the one I got from RGEO Rick. This process is completely dependant on the shaft, because that's what you're "registering" the arm's balance against. If the shaft is not true/straight/round..."fuggedabowdit" as they say in Brooklyn!
You need to go slow, check and recheck as you drill...BE CAREFUL when you drill if you're using a hand drill instead of a drill press and a jig to remove material. One slip and all your hard work is for nothing! You also have to understand that mass produced factory arms will not have the kind of attention paid to balancing as you can apply. I'm not talking about balancing services, you expect them to "get it right", but when there's several hundred arms to be balanced, they're more likely than not going to go for..."meh...that's good enough"! In any case, this arm was pretty easy to balance and you want to get to the point where the arm will roll super slowly from one end of the razor blades to the other with the slightest itty bitty nudge, and not loping past one pole as if that one might be a bit "heavy". That's exactly what I got here, and I was very satisfied that balance was good! If the arm is as good as you can manage, I figure you should be confident enough to put your name on it. I don't do that if it's sent out for dynamic balancing because I figure I might just screw things up. With static balancing, if I have the slightest suspicion that one pole or the other just might be a teensy heavy, I'll engrave that pole as "insurance".
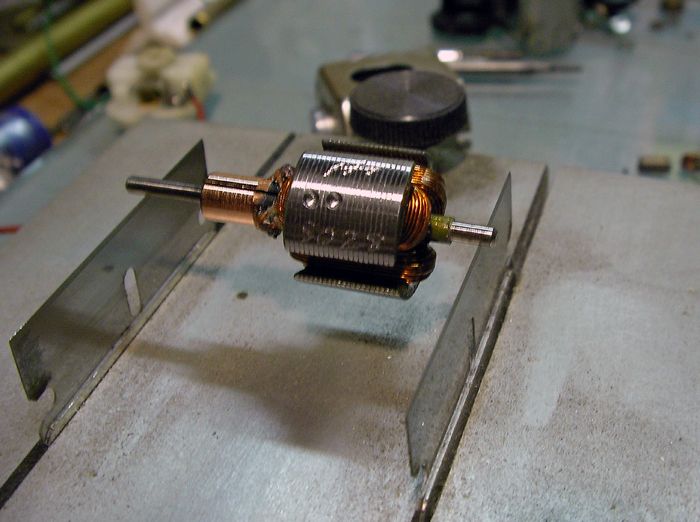
So with the arm done, it's time to head back to the setup and finish that off. Even though the "hole" was fairly tight stock, I whipped up a pair of .004" shims to see what those would do. ***On setups like the Mabuchis where the magnets are held in by one clip and a set of tabs on the other side, too much shimming will result in the magnets being closer on the clip side than the tab side, because the tabs will only let them move inward so much. From what I've seen, .004" shims are thin enough to not cause that to happen. If you need to shim much more than that, it might be time to flatten the magnet retainer tabs and go with two spring clips so everything remains concentric as possible. Anyway, I wound up with a total difference of .024" (.012" per side) after shimming, which is fine for these fairly imprecise setups. The math sounds OK, but the reality is that you could wind up with more on one side and less on the other, even though the Mabuchi cans are generally really well formed. Another potential problem is that the bearings in these things are NOT precision pieces 
While everything was apart and the magnets were out of the setup, I took the opportunity to drill the can and end bell for screws. Those tabs WILL break, may as well take care of business beforehand and act preemptively. I know they're not "correct", but the Mura 0-56 screws are the best. They're small enough to not interfere with most installations, very strong and...er...I like the way they look
Anyway, you also need to remove any burrs from inside the can after drilling and get any steel drillings/filings out of there before final assembly.
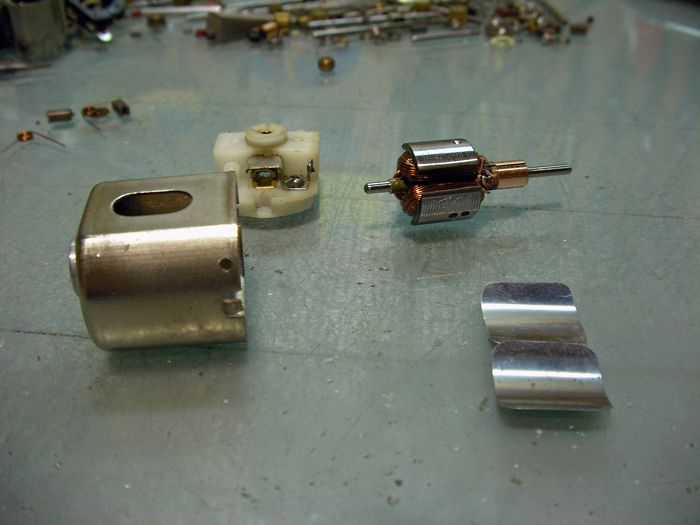
Now, with the final assembly done, it's time to make some adjustments. Of course, beforehand, you need to be sure the brushes DO NOT get hung up on the tubes. They should fall out of the end bell by just gravity, but not be sloppy either. I tested the arm first with the stock springs and it draws just under an amp at 6VDC, but seems like it could use a bit more spring tension (I'll sometimes use a toothpick to put a bit more pressure on each side to see how the motor "likes" that). So I decided to go with a pair of Mura extra light springs, which are a little stouter than the stock ones, but not THAT much. Also, with these small brushes, the amount of pressure per square unit of measure will be greater than with the larger 36D size brushes. Imagine a woman stepping on your toe in flats...and then the same woman stepping on your toe in 6" spiked heels, uh...you get the picture of the physics involved
Anyway, going with the Mura springs which have a larger diameter at the coil, I installed a set of post protectors...not so much for the heat because the motor doesn;t get too warm at all, but because the springs fit better with the larger diameter posts.
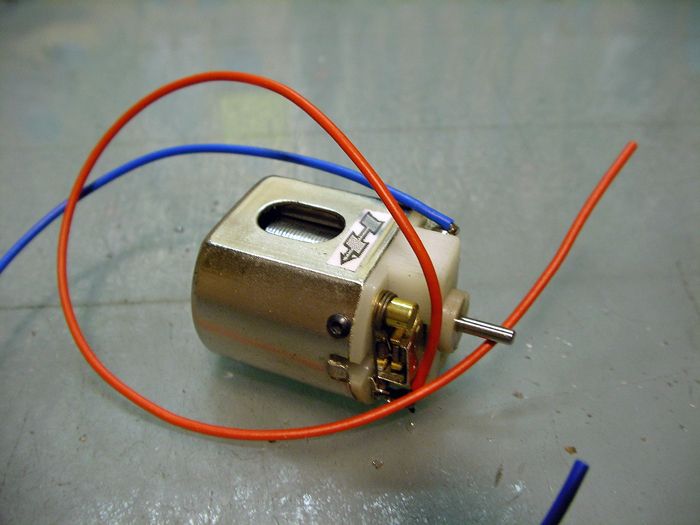
Result? The motor is a screamer (relatively speaking) drawing just over an amp and running nice and smooth thanks to investing the time to get the balance as good as possible. I also spent the time to get the arm as perfectly centered in the field as possible. Install the arm with no brushes and no spacers...give it a spin and see where it "lands". Add some spacers and try again, until there's as little "slop" as possible without the arm being bound AND it's not pushing towards one end or the other. It should spin freely and not "want" to be closer to the end bell or can end.
With everything as good as you can get it, install some new leads and put your name on it...I call this one "done". Lastly, when installing the leads, I like to install the bottom lead from the inside of the tab and heading up where it will need to go when installed in a chassis. Whoever installs the motor may just say "thank you" when they notice that 
-john