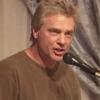
#2801
Posted 01 May 2011 - 09:21 PM
-john
#2802
Posted 03 May 2011 - 10:51 AM
John, I was finally able to build a car for the Kemtron rewind you did for me. As you might recall, one of the arms was bent, so I used the other setup that you had assembled and built a hardbody chassis for it. The motor runs awesome, pretty close to some of the six volt Kemtrons I have, only much smoother. Thanks for your craftsmanship on this motor.
Best regards
Jeff Buyer
Requiescat in Pace
#2803
Posted 03 May 2011 - 01:42 PM
-john
#2804
Posted 03 May 2011 - 02:31 PM
Hi Jeff...wow, I didn't remember doing any 5-pole arms that actually worked!? Jeez that's a surprise...no...really! Anyway, I was able to get that open frame motor apart you sent and clean everything up to reuse. It was tough to get the epoxy off the arm and still save the com. It's a small com with a hole for a 36D sized shaft, so it would have been difficult to replace the thing. So far...so good and now I just have to come up with a 1 ohm wind to match what was on there. I'll keep you posted.
-john
The one you did with the slight bend in the shaft works well, too, although I had to use an endbell with the timing adjusted to get some speed out of it. That arm might work if I put the gear on the other side. So basically both 5-pole rewinds were a success.
JB
Requiescat in Pace
#2805
Posted 04 May 2011 - 10:29 AM
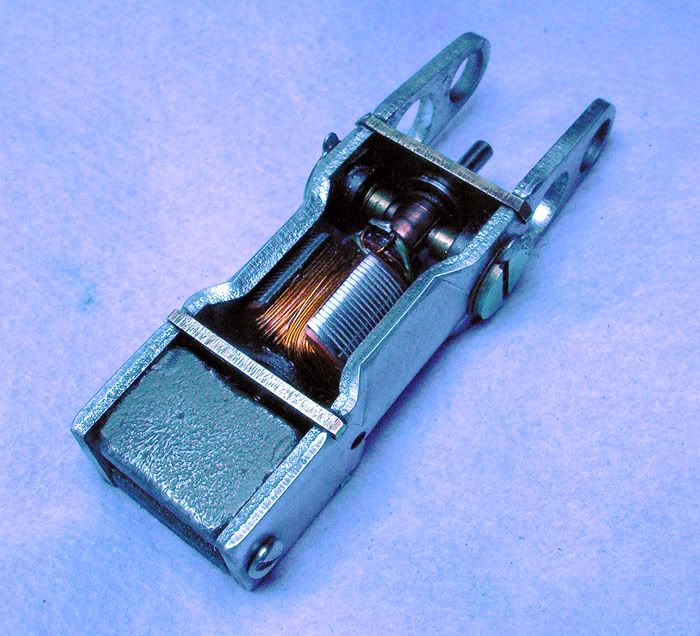
-john
#2806
Posted 04 May 2011 - 10:45 AM

BTW- Bill Fernald is coming over next week to work with me and start teaching me rewinding. I'm super stoked to get started !!

I'll try and keep you posted on how things progress as we move along.
I also have another question for you John. What do you use to test the arms? Just a reg ohm meter ? and if so, where can I get a good price on one ?
Thanks John for all the help, and all the great info you take the time to share with all of us.

Vic
#2807
Posted 04 May 2011 - 10:55 AM
The brushes on that motor won't survive a full race, sadly on that wind. I never did come up with a good solution.
Hotter than a 34 needed different springs, in this case, threading in a second spring inside the first to double the tension was required. But then the brushes would wear down very quickly. But I never found a satisfactory solution.
Fate
3/6/48-1/1/12
Requiescat in Pace
#2808
Posted 04 May 2011 - 11:28 AM
Don
PS: John, I may have some 33 or various other sizes lying around if you want some - just let me know!
#2809
Posted 04 May 2011 - 11:49 AM
Hi Jeff...thanks again for the info! Your next one is done and I was able to strip it and rewind it without too much trouble (except for the epoxy that was on there). The thinnest wire I keep here is #30, so I tried stripping a Mabuchi and reusing the wire but got inconsistent results on the meter. I then did a #30 wind (lots of turns on that short stack) and it came in between .8 ohm and .9 ohm. The magnet on the motor is dead as nails and I couldn't get a reading much past 100...so it will need to be either zapped or replaced. I cleaned the motor up a bit but didn't cut the com as I wasn't sure how much was left on there:
-john
Nice work, John. I'm curious if you used the original springs, or the extras that I sent? One of the originals had cooked, so it's weaker and might not apply the right tension.
JB
Requiescat in Pace
#2810
Posted 04 May 2011 - 02:09 PM
BTW- Bill Fernald is coming over next week to work with me and start teaching me rewinding. I'm super stoked to get started !!
![]()
I'll try and keep you posted on how things progress as we move along.
Please do Vic. Be forewarned that, even with some missteps (maybe I can help you avoid some of the ones I've made)...this stuff is like crack, not that I would know

I also have another question for you John. What do you use to test the arms? Just a reg ohm meter ? and if so, where can I get a good price on one ?
All I have is a decent multimeter Vic, but it can only resolve to tenths of an ohm, and not that accurately. Accurate milliohm meters are expensive and impossible for me to justify on a hobby budget.
The brushes on that motor won't survive a full race, sadly on that wind. I never did come up with a good solution.
Hotter than a 34 needed different springs, in this case, threading in a second spring inside the first to double the tension was required. But then the brushes would wear down very quickly. But I never found a satisfactory solution.
Fate
Yes, I pretty much figured that might be the case Rocky. The motor was cooked in any case (maybe partly because of the magnet), so Jeff can figure how he wants to proceed.
PS: John, I may have some 33 or various other sizes lying around if you want some - just let me know!
Thanks (as always!) Don. I rarely even use #30 wire except on double winds. If I had a bunch of these things to do, I'd just get a roll of #33 or #32. A one pound roll of that gauge is probably thousands and thousands of feet long. It's such a rare thing (so far anyway) that I need to use such small wire it seems a waste to have it sitting around.
Nice work, John. I'm curious if you used the original springs, or the extras that I sent?
Thanks Jeff

-john
#2811
Posted 04 May 2011 - 02:32 PM

I intend to live forever! So far, so good.


#2812
Posted 05 May 2011 - 12:16 PM
Ya, that lump of iron really benefits from being regularly zapped.
As for the motor, My late Friend Jose Rodriquez jr who was the impulse behind the Atlas stuff (he once sent me sketches of proposed motors they decided to NOT build) that the 6 volt arms were huge failures. The odds were 50% that the wind would blow within the first couple minutes of getting power the first time!
I have some 208s and 206s that have 40 years on them, but it took a lot of work. But that is outside the scope of John's winding thread.
You might not know that there was a version of the 206 with overhead brushes and normal springs like a pittman 196. THAT layout is so much better for this motor from a reliability standpoint and will work better with the rewinding as well.
Fate
3/6/48-1/1/12
Requiescat in Pace
#2813
Posted 05 May 2011 - 08:17 PM
Jeff, if that's an Alnico magnet, try to zap it before you replace it. That might be all it needs, Alnicos are known to weaken when an open frame motor is disassembled.
I plan to do just that, but I do have a NEO ready to go in this motor that I want to try as well.
Requiescat in Pace
#2814
Posted 07 May 2011 - 08:17 PM
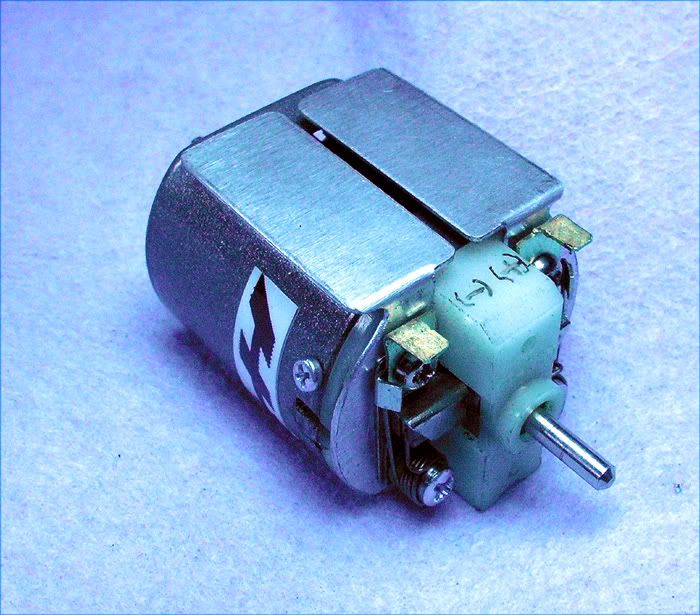
The arm was a Tradeship blank that I added a big ol' honkin' Kirkwood com to after reaming it out to fit the larger shaft. The wind is a #29 double and while the setup can probably take a #28 double, I figure a #29 double will run cooler and last better. The motor does run fairly cool and revs very nicely. The elephant ears aren't "necessary" but I always wanted to do a set for a Mabuchi and they sure can't hurt. Besides, I think they look cool

-john
- MarcusPHagen likes this
#2815
Posted 07 May 2011 - 10:16 PM
I track tested the Speedy Gonzales Buzco car today.
The Havlicek motor performed perfect.
It runs cool and smooth. Exactly what I wanted.
Mission accomplished, Thanks John

Paul Wolcott
#2816
Posted 08 May 2011 - 07:24 AM

-john
#2817
Posted 08 May 2011 - 04:01 PM
barn
Barney Poynor
12/26/51-1/31/22
Requiescat in Pace
#2818
Posted 08 May 2011 - 04:17 PM
Just the offer is a stunner. Of course you're always welcome for the motors and I'm stoked to have them in any Team Cort cars too!
-john
#2819
Posted 08 May 2011 - 05:07 PM




My life fades, the vison dims. All that remains are memories... from The Road Warrior
#2820
Posted 08 May 2011 - 05:22 PM
I remember too...and I also remember that you were among the first to be really supportive and helpful. There were also others who probably thought I was strange because after all, why would anyone want to wind an armature when people just bought them and threw them away (even whole motors!). In fact some pretty much said that

Now the tables are turned and I'm just amazed how these motors turn out.
Not at all Gary...I still learn every time I do an arm or build a motor! I may never "get there"...but I am enjoying the heck out of the journey.
It looks like you were "born to wind"!
I don't know Gary, I think that a LOT of people would be doing what I do if they gave it a try and stuck it out a bit. In fact I'm sure of it because, after all, every other kid in the 60's had a LaGanke and spools of magnet wire!
-john
#2821
Posted 08 May 2011 - 05:35 PM

Havlicek rocks.
- MarcusPHagen likes this
Paul Wolcott
#2822
Posted 08 May 2011 - 05:55 PM
-john
#2823
Posted 11 May 2011 - 02:26 PM
Removing the caged bushing in the can and installing a bearing is pretty straightforward in a Mabuchi...but it's the endbell that really needs "surgery" to get a bearing installed. The bushing pocket is just too small for a snap-in replacement. So the end strap needs to get cut in the middle and a bearing-carrier strap installed. I used tool steel this time because...well...just because it was within arms reach. I've used brass before and it works well too, although I guess steel is better. This would almost definitely be MUCH better and more accurate with a drill press, but I was able to get it done with a bunch of fiddling and squinting. The bearings are well aligned now as the armature will slide easily in the setup. So after all that, I can now start making up an arm and get to winding. Best part, the arm spins for days in the setup and smoooooth!
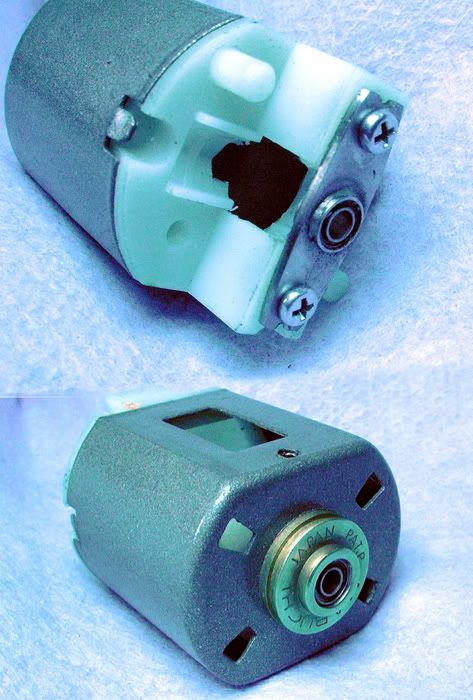
-john
- MarcusPHagen likes this
#2824
Posted 11 May 2011 - 03:23 PM

It gives me goosebumps.
One of these days I'm going to ask you to wind me up one just like that,
really really hot and dangerous.


Paul Wolcott
#2825
Posted 11 May 2011 - 04:51 PM

-john