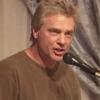
#3426
Posted 07 March 2012 - 06:59 PM
Question please?! As an example, you wind two of your three poles on the motor arm and you are about to wind the last pole. You look at the remaining length of wire and notice that it isn't enough to finish the wind. Can you solder the wire of the last pole wind onto the comm tab, cut off the remaining length of wire, take the new roll of wire and solder that end onto the previous comm tab where you left off and continue to finish the wind without compromising the motor performance?
Though the wire was cut to finish the wind, wouldn't the soldering of the wires onto the tab still make for electrical continuity and not affect performance?
I'm just trying to figure this out please.
Thank you for your time.
Ernie
#3427
Posted 07 March 2012 - 08:41 PM
This can be done, as a matter of fact some I knew did this just to make sure each coild of wire is the same length, however, DO make sure you solder(braze is better) and wrap the com and wires VERY well, then do a good epoxy job on it....Kim
#3428
Posted 08 March 2012 - 06:16 AM
What Kim said

-john
#3429
Posted 08 March 2012 - 09:53 AM
Thank you for the great info! It's appreciated.
Ernie
#3430
Posted 08 March 2012 - 11:44 AM
Just thought I'de throw that in , thought it would help.
- MarcusPHagen likes this
Pro motor and car builder
Australian AA/FC quickest car
#3431
Posted 09 March 2012 - 10:10 AM
That sounds like a great tip (pardon the pun -hahaha)!
Would you have a photo of your wedger so I can better understand what it should look like please?
Thanks.
Ernie
#3432
Posted 09 March 2012 - 03:00 PM
Keeping the same number of turns per pole goes hand in hand with a nice neat pattern and this is the real consideration. The length of wire idea then becomes a dim second thought that has no real bearing on the arm being wound.
Using more than one piece of wire, as John mentioned, is acceptable with no problems at all. It is another matter, as to how you messed up in the first place, having to resort to the second wire.
Dan
.
#3433
Posted 09 March 2012 - 04:34 PM
-john
#3434
Posted 10 March 2012 - 12:47 AM
Pro motor and car builder
Australian AA/FC quickest car
#3435
Posted 10 March 2012 - 07:14 AM
-john
#3436
Posted 10 March 2012 - 12:21 PM
Pro motor and car builder
Australian AA/FC quickest car
#3437
Posted 12 March 2012 - 02:19 PM

You have great control of tension and it allows you to put the wire exactly where you want it. I have a rotating fly tying vise that I held an arm blank in. I did wind one arm then pulled off the wire to do it again, but haven't gotten back to it after about a year. My ceramic bobbin worked great with the #29AWG wire I used. Of course, after tying thousands of flies with one, I'm used to using it! I didn't rotate the arm much, just wrapped like I would with a fly. Very fast easy way to put the wire on IMHO. I just need to find time to do it. And find some .490" blanks and capped comms. I would love to wind my own Euro arms. Even if I have to send them out to be epoxied and balanced.
#3438
Posted 12 March 2012 - 03:34 PM

Tension needs to be pretty significant and consistent, but also needs to change for different gauge wire. By setting "drag" on your crank, you can "feel" how much to tension the wire without breaking it. That's just me though and whatever works for anyone is for sure "the right way"!
-john
#3439
Posted 12 March 2012 - 03:42 PM
Honestly, I can't imagine anything working better than these:
Tension needs to be pretty significant and consistent, but also needs to change for different gauge wire. By setting "drag" on your crank, you can "feel" how much to tension the wire without breaking it. That's just me though and whatever works for anyone is for sure "the right way"!
-john
Actually John, that is why I like the bobbin. The tension is maintained by gripping the spool of wire (or thread in the case of flies) between the palm of your hand and your pinky finger. Then you grip the tip of the bobbin between your index finger and thumb to move the tip of the bobbin to where you want to wind. It is a very natural movement when you get used to it. And believe me, you can get to the point where you can tension a very thin thread to just shy of the breaking point very consistently. Granted you have to move the wire to a spool that will fit in the bobbin, but I don't see that as a big deal. The other thing I like about the bobbin, is my fat fingers don't fit between the stacks, and the tip of the bobbin tube does

#3440
Posted 13 March 2012 - 05:18 AM
That's just me though and whatever works for anyone is for sure "the right way"!

-john
#3441
Posted 16 March 2012 - 09:07 AM
The bobbin idea would sort of pile up the wire on the blank. It is limited in placement of the wire and would only make the arm look somewhat machine wound. If your goal is to save time, fine. As the wire diameter increases, the bobbin becomes more useless.
If you want to create a nice armature, hand wind it. Simple wood Popsicle style sticks, rounded off small screwdrivers and a few other trick tools help much more than a bobbin ever could.
Along the same lines, any tension device would just get in my way.
Use your hands.
Dan Miller
.
#3442
Posted 16 March 2012 - 02:16 PM
-john
#3443
Posted 16 March 2012 - 08:48 PM
We used the cap of a BIC pen (pocket clip end) to manipulate the wire for the patttern that was being wound.
I would also protect the tip of my finger with machinest tape. It was a must when winding hundreds of arms per day.
Dan Miller, how have you been? It's been a long time. . .
"Racing makes heroin addiction look like a vague wish for something salty" - Peter Egan
#3444
Posted 17 March 2012 - 07:48 AM
Sometimes small slices of plastic credit cards can be handy to have.
Also use #11 X-Acto blades and can think of no substitute.
John Miller,
I am doing OK. Right in the middle of making some new armature lamination dies. They will be run on the same punch press I bought from Ray while you were working with Fantom and ProSlot .
Also making my own commutator as the RJR - Bill Bugenis machines ended up 8' underwater. Very busy at this time.
Dan Miller
.
#3445
Posted 17 March 2012 - 03:22 PM
Are you saying you through them in the ocean or a river or you got hit by a flood ? why would they end up under water ?
Whats the chances of getting some .435 Dia arms made ?
Pro motor and car builder
Australian AA/FC quickest car
#3446
Posted 17 March 2012 - 05:14 PM
Hurricane Irene flooded Lou Pirros shop. The machines were in the rear of the building.
No chance on .435" arms from me. Way too small to be effective.
Dan Miller
.
#3447
Posted 17 March 2012 - 07:44 PM
I intend to live forever! So far, so good.


#3448
Posted 17 March 2012 - 08:36 PM
Thats pretty bad
So does that mean that Bill doesnt have any more comms ? or it was just a machine you got from him that you used to make your own comms ?
Can I suck on your brain a bit more and ask , why is .435 to be effective , I've never had one but I was thinking of using one in a 12 segment Neo open drag motor .
Also in your mind what would be more effective and why ?
I have a felling I wil be hanging on ever word you say hear .
Robert K
Pro motor and car builder
Australian AA/FC quickest car
#3449
Posted 18 March 2012 - 08:01 AM
Bill has tons of commutators. Also suggest that he will rebuild his machines over a period of time. I used to mold my own commutators, on the machine Bill now has, for some years, when it sat in Kokomo Indiana at RJR. Bill was nice enough to let me mold a batch last Summer, just before the flooding hit.
In regard to .435" arms, I spoke out of turn, as I know pretty much nothing about armatures for Drag use. Played around some years ago. Ran under 3 class records in testing and let it go.
Check with ProSlot. My guess is that you need a certain amount of wire, on the first layer of the arm, to make it an effective armature for Drag use. Your .435" may limit that feature. If it was reasonable to assume that a Drag arm, made that small, would be a good thing, then the ProSlot guys would have already done something about it. Maybe like testing wire EDM or Laser cut laminations that size, to see how that small size range arms would work, then moving into production of such an armature, if it had proven itself.
I do know that ProSlot is involved in a small diameter Eurosport armature effort. Maybe they are playing with small diameter Drag arms as well. Would not suprise me to find they have already been down that road.
Dan Miller
#3450
Posted 18 March 2012 - 04:54 PM
Getting 7 winds of 23 gauge is fairly simple on a .445 arm but yeah like you said it could become a bit of a problem with a shorter stem.
I was sponsored by ProSlot for a while there until I lost it with a guy on a different forum and really put my foot in it so I don't think they will be to keen to help me out there , I've only got myself to blame there.
Because drag racing only goes for a very short amount of time I am going to try some arms with the 105°C Enamaled copper wire for my next attempt.
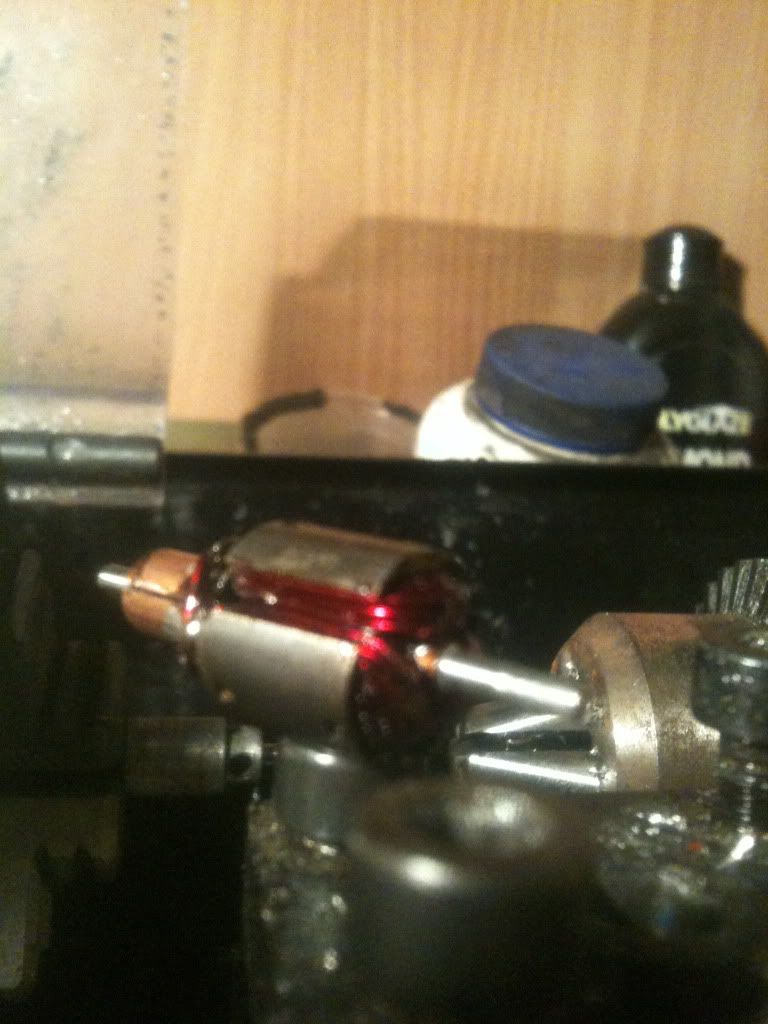
Not the best photo but thats the first test subject.
Pro motor and car builder
Australian AA/FC quickest car