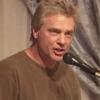
#101
Posted 08 November 2008 - 05:10 PM
-john
#102
Posted 08 November 2008 - 05:46 PM
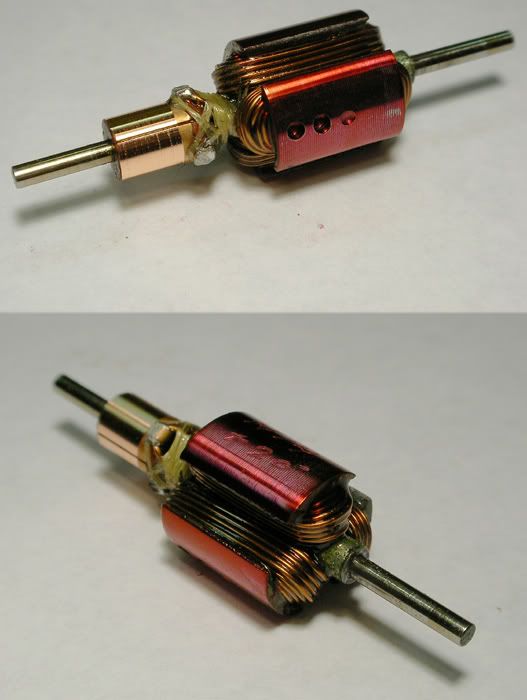
-john
#103
Posted 08 November 2008 - 08:40 PM

Michael Rigsby
"... a good and wholesome thing is a little harmless fun in this world; it tones a body up and keeps him human and prevents him from souring." - Mark Twain
#104
Posted 08 November 2008 - 09:29 PM

Now THAT one is beautifulllll....You out did your self. A CNC winder couldn't do any better....NICE
PHIL

#105
Posted 08 November 2008 - 10:28 PM
Remember, two wrongs don't make a right... but three lefts do! Only you're a block over and a block behind.
#106
Posted 08 November 2008 - 11:20 PM

Jairus H. Watson
3/12/59-5/19/25
Requiescat in Pace
#107
Posted 09 November 2008 - 06:27 AM
Michael,
At this point, I'm almost embarrased to say how much time and effort goes into one of these things...not to mention material costs. I'm even more embarrased to say I'm still working on improving these things



Phil,
The visual difference in this arm is due to the different pattern I used. It's not as efficient at making use of the available space on each pole and places the coils further away from the pole face on each succeeding layer so I don't know that it has any mechanical advantages, but it makes the top and bottom of the poles neater. The sides of the poles are the easy part

Tex,
Yup...American horsepower, East Coast style (although I hear everything's bigger in Texas!)

Jairus,
Thanks buddy. It's a real retro amp-sucker.


-john
#108
Posted 09 November 2008 - 09:34 AM
Thorp used Perolithic spacers between the stacks. (I can send you a picture if you like.
Certus used sheet metal drills for balancing and green colored end of stack spacers for instance.
It would be really cool to gob up a lesser looking wind with some green gooey epoxy and make a vintage looking bubble gum arm that WON'T blow apart.
Bet we could get some of the vintage arm winders to chime in on the details and provide pictures.
Jairus H. Watson
3/12/59-5/19/25
Requiescat in Pace
#109
Posted 09 November 2008 - 10:31 AM
I figure that it would be cool to someday have my arms be recognizeable...maybe even desireable (hey...you never know!) on their own. I always put the "H" thing on them for that reason. I'm not really interested in trying to do replicas, and the great winders of the past arms stand on their own today as well as they did decades ago although they're probably getting a little fragile at this point. If someone wants an arm wound or rewound, all they have to do is ask...but it will come out looking like one of mine in the end


-john
#110
Posted 09 November 2008 - 11:10 AM
I don't know about survivors. The "Plus/Minus" of then was that any arm was probably being run that weekend after being done, if it worked it got raced once, twice at best. If it didn't it got stripped or tossed. I have a couple surviving NOS arms from when the last local raceway suddenly crashed, and by the time I moved to Denver, no one was running G.7s. Later P and strap cans with the different interal sized weren't using the old 512s we were building.
I can LOOK for oldies, being a pack rat, but I am not sure. I still have blanks and spacers and the like, but not sure about others.
Fate
3/6/48-1/1/12
Requiescat in Pace
#111
Posted 09 November 2008 - 12:32 PM
I can certainly understand your wanting to forge your own path and reputation. In my humble opinion, you are doing just that.
What I was suggesting is what has happened to me... in that, my skills have been utilized replicating vintage paint and chassis. In some cases requested without my mark/signature! Just one feature of my services only, not the only talent I have in my arsenal. I still paint and build to my own drummer....
I know you and I have talked about this in PM's, I was simply bringing it out in the open to see what the board felt.
Now, I will shut up about it...

Jairus H. Watson
3/12/59-5/19/25
Requiescat in Pace
#112
Posted 09 November 2008 - 01:06 PM
I still see a bunch of absolutely gorgeous arms in Rick's builds and others from time to time. They're apparently still "out there", but after three or four decades are probably getting a bit fragile.
Hi Jairus,
I totally understand what you're saying and sure appreciate the insight. Still (and like the song says)..."I gotta be me"

-john
#113
Posted 21 November 2008 - 03:14 PM
Question, how do you solder the wires to the com ?
That was what always seemed to be the issue for me, in the end we just ended up crimping and not soldering.
#114
Posted 22 November 2008 - 08:08 AM
Arm winding has been a real "journey" this time around for me. Just finding a high temperature epoxy that was available in small quantities was a problem. On the com tabs, I've been using silver solder...being careful to scrape away the insulation from the magnet wire where it passes over the tabs. Still...I had an arm fail recently for someone I sent some to exactly at the com tabs. I haven't seen the arm afterwards, but tend to think the solder joint must have been bad rather than the solder actually having melted off the com tabs. I went back and looked at how I solder the tabs (I also crimp them before soldering) and have started to tin the inside of the tabs before soldering as a way to make sure that there is a solid joint. With not enough people using my arms to get a sense of whether this will make a difference, it's hard for me to know whether I'm on the right track. There's another person from here who has done some slot drag racing with a couple of my hotter arms and hasn't had failures...but those runs are very short.
Of course, the best way to make this connection would be to crimp and weld but I haven't been able to come up with an economical and reliable/repeatable way to accomplish this. The precision welding machines I've seen that are used for this application in industry are very expensive and rather large. There are many homemade spot-welding rigs out there that people have put on the web made out of various found items like discarded microwave oven transformers and car alternators with motors driving them that aren't applicable for various reasons. I even posted a question at a welding forum for hobbyists and (I think) pros...but got no response. I think because this is very different from welding a garden trellis or heavy gauge steel machine parts. This is a low-amp and precise (the parts are very small and made of brass and copper) application that I don't think many home-welders would even be interested in. The best (especially in this economy) solution would be some sort of homemade device that's small/cheap/controllable and will produce repeatable results. If it's out there...I haven't seen it, but I'm looking!
-john
#115
Posted 22 November 2008 - 11:17 PM
The guy that Stoo talked about had some method using a carbon element and silver solder wire ground to a point. I once spoke to one of the better arm winders around and he while not giving too much away said that he basically had an alloy heat sink that the com sat in that just left the tab exposed.
I would expect that something could be built along the lines of a pulse circuit to fire a relay using a carbon element (link inside some soldering irons) and a lot of amps (car battery) alloy heat sink and basically the silver solder (hard) as an electrode gound to a pin point.
Just a thought
#116
Posted 23 November 2008 - 11:31 AM
I can envision such a thing, but don't have the electronics knowledge to build it without an "electronics-for-dummies" set of plans. Eliminating the car battery would be nice also for obvious reasons and the online plans for DIY welders using an old microwave oven transformer seem like a good way to go in that direction. What would be REALLY trick would be to somehow use a power supply such as the Trinity iPower I have. While voltage is low (same as a car battery)...there is up to 15 amps available, which is pretty significant. I don't know if that would work, but it sure would be cool for this application...sort of the same way the iPower (and similar supplies) can power other tools such as a com lathe. Since we're talking about very small spot welds...it seems reasonable???? This is where we sit back and wait for the electronics gurus to help out...anyone?
-john
#117
Posted 23 November 2008 - 11:53 AM
Maybe an actual stick welder might be a better start, what we do is use it as the source and via relay just produce a controlled pulse of high amp power, I am expecting this will be all over after 10 milliseconds. Key thing would be to build a alloy heat sink for the com that just exposes one tab, with enough room to get a carbon heat source and a silver solder elcetrode on the tab, then foot contol switch to fire off the spot weld.
You need to get this very hot very quickly, which I think will need more than 15 amps.
Stoo if u read this what did hutco do.
#118
Posted 23 November 2008 - 12:00 PM

-john
#119
Posted 08 December 2008 - 07:37 PM


-john
#120
Posted 08 December 2008 - 08:04 PM
Dinner or lunch?

Jairus H. Watson
3/12/59-5/19/25
Requiescat in Pace
#121
Posted 09 December 2008 - 01:28 AM
Yeah, the Thing Hutcho used to Use, was also Somewhat Crude and Typically Brutal, Dangersous and Overkill in the Way ONLY Hutcho could be !!!
Like Lindsay was suggesting, Hutcho, used to Weld all his Coms, as Lindsay suggested, with a Certain type of Solder that he had sourced, that was a Particular type of High Temp stuff.
It May have been Silver Solder, but I seem to Recall, it was a kind of Dull Grey in Colour and was Very thin.
I Will have to ask him,..Heck as Hutcho IS rather computer literate, I will have to send him this Link, as I am SURE He and John could have a Great Chat !!!,..ROFL
Truly guys, Steve Hutcheson IS one of the Greats, the level of his workmanship and his creativity and innovative thought from Waaay back was a joy to behold and I Have NEVER driven Anyones Slot Car Motors that came Anywhere Near Steve's, Lindsay Can Vouch for that as I am sure So can almost anyone who raced against them !!!,..lol
Steve's machine actually used a Rather Large Old Welder, With Scary Capacity.
The Arm was Held in a Block/Jig he made for the Purpose, in a Vice, and actually Really Required Two people to use it, (I think he used to have it set up, but the last arm he did for me was done this way and he even welded some Pinions on for Fox when he kept melting them off !!)
He had as you say a Shaped Carbon Tip, that was applied to the Com, with the Ground being made through the Jig/Vice.
This was the Tricky Part, as One had to get the Timing AND Attachment and Removal of the Right Contact FIRST, or one could Blow the Arm/comm to Bits !!
All in all a Rather Scary and tricky Operation, which Hutcho seemed to Carry out in His usual Adept style !!
AND, this was Waaaay Back when Lindsay and I were just Kids and Even arms from the States were Just starting to be Welded.
Hutcho didn't Lose too many arms !!
I always wondered what some of his Motors would have been like Dynamically Balanced,..Mind you though, Much like John, I think Hutcho Kind of Had a Magic Touch with his Static Balance, as they Were Majic Motors and any arm he did for me, Sang Like a Bird !!!
Hey John, I have found one of My Older 1970's Chassis, One with Nickel Silver Pans which Lindsay probably remembers, and an almost New, (in fact the Can bearing hasn't even been soldered in) Green Can and endbell, so Perhaps I will have to Try and Melt the Solder off one of your Arms sometime !!!,..lol
Oh and send you one of Mine ofcourse !!,..lol
Stewart Amos
Old Racer from Sydney, Australia
FASTUFF Race Proven Products
https://ascra.au - Australian Slot Car Racers Association
#122
Posted 09 December 2008 - 06:40 AM

Hi Stewart,
The power supply I'm using is actually an automotive battery charger/motor starter. For the com connection, I've fashioned a sort of split-ring collar out of aluminum and the part that slips over the com has fins so it can act as a heatsink as well as an electrical connection. The outside of the piece is where the battery clamp from the starter attaches and the pressure from the clamp tightens the thing onto the com. For the other connection, I'm using the carbon rod from a carbon/zinc "D" cell battery (they're getting hard to find). I'm going to try some "C" cell maybe even "AA" cell rods if I can find them. I also had tried some fat graphite rods from large round pencils. They work also, but are fragile and the material doesn't work as well as the carbon from the batteries.
Part of my confusion here had been with the term "welding" the com tabs. Welding usually refers to applying enough heat to fuse the base metals with or without a filler metal. Spot welding (at least as far as I had known) refers to fusing the base metals directly with no filler metal by applying a short burst of heat to a point (electrical). While the process here is really silver brazing or "hard silver soldering". To add more to the confusion, this is really different from regular soft silver soldering such as what slot car builders use for some chassis work (around 400°-450°F using a solder alloy of between 2 and 5% silver). This stuff (hard silver soldering/brazing) takes place at around 1,200°F and is more like what is used for jewelry and some dental work.
Then there are a few "in between" materials like "Solder-It" paste which is a paste of silver alloy and flux that will melt at 450°F...but remelts at over 600°F. Often the difference between brazing and soldering as I've seen them defined on the web is only one of temperature...soldering being a process that takes place up to around 400°F-450°F, and brazing anything above that. Again, you can find different people using the terms "welding", "brazing" and "soldering" almost interchangeably and even web definitions vary

People also need to be a little careful when choosing silver wire (there's also silver paste with powdered silver and flux for approximately 1,200°F brazing) since some grades also have some cadmium in them. Even though these connections are very small, cadmium produces toxic fumes when heated. Using pure silver wire and good ventilation seems preferable although it will take a bit more heat.
I'm sure the manufacturers have dedicated machines made for this process and they may even be doing actual spot-welds (?), but this all seems to be working fine as is. It would be really nice to install a timing relay on the power unit as has been suggested to get more uniform results, but I haven't a clue as to what relay to buy or how to install it, so I'm probably just going to continue doing this as I have been for now. Heat is sufficient to melt copper and brass if applied for long enough, but getting things heated sufficiently to melt the silver without melting the brass/copper isn't too hard so far (about a second or two of contact).
-john
#123
Posted 09 December 2008 - 08:22 AM
Don't know if it will be of use to you or not, but check here for jewelers solder and supplies. Look under the Jewelers supply tab and on the next page about three quarters of the way down on the right column you'll see the solders and pastes listed. I also reccommended this site to Rick B. for ceramic polishing media for tumbling since they are a lapidary and jewelers supply house, but they carry a nice selection of silver solders of varying melt temps at decent prices. If nothing else, it will be another source you can use. Also check out page two on soldering tools. They have a flameless soldering machine listed there that is somewhat like you are talking about for doing high temp jewelry brazing. May be just what you are looking for. Looks like it would work ok.
You make some of the most beautiful winds I've seen. Maybe one of these days I could afford to have
you wind me a custom X-12 arm.
Michael Rigsby
"... a good and wholesome thing is a little harmless fun in this world; it tones a body up and keeps him human and prevents him from souring." - Mark Twain
#124
Posted 09 December 2008 - 08:54 AM
Now there's a thought !!
I have a Heap of the Shorter Mura Blanks,..Whats a Custom X-12,..??,..ROFL
Heck for that Matter What Turns/Wire does an X-12 use anyway?
Answered myself, 50/29#
Stewart Amos
Old Racer from Sydney, Australia
FASTUFF Race Proven Products
https://ascra.au - Australian Slot Car Racers Association
#125
Posted 09 December 2008 - 10:34 AM

On the arm thing, you'd be surprised at how cheap my arms are

-john