Well thank goodness I asked I'll remove the bulge.

R&C Pablo Grand Prix entry
#101
Posted 28 October 2013 - 08:52 PM
Paul Wolcott
#102
Posted 29 October 2013 - 08:56 AM
Thank goodness the powerplant is done ! What a struggle to do the arm. I gotta get a drill press.
I had 2 problems with arm #2 - the heavy pole was so heavy I couldn't drill enough to make it perfectly balanced, and ran out of room for more holes ! Didn't want to make the same mistake and drill too deep, so I quit while I was ahead. It's balanced OK but not great.
2. I nicked some winds in one spot and that could cause a failure down the road. But, it is running right now and I must move on. If it fails later, I'll just change the arm. Runs really cool and sounds fairly smooth.
Paul Wolcott
#103
Posted 29 October 2013 - 09:30 AM
I also found two different "green comm. end" arms. The one in my Cox 150 had a comm. with open slots like current motors. The other one I removed from a mustard colored can had comm. slots that were filled in with the green plastic. While both are period correct I'm guessing the one with the open slotted comm. is best, right?
#104
Posted 29 October 2013 - 10:01 AM
I know you're "moving on" to the next step, Pablo, BUT....... if you ever feel like tweaking that arm a little more, perhaps you could ADD a little weight to the other poles to get it balanced(?). How? I dunno.... brush on some extra epoxy(?).
Remember, two wrongs don't make a right... but three lefts do! Only you're a block over and a block behind.
#105
Posted 29 October 2013 - 11:58 AM
Already did that. Still slightly heavy on one side.
The real show stopper would be if the arm shorts. It seems to run fine as is.
Paul Wolcott
#106
Posted 29 October 2013 - 03:47 PM
You COULD try to balance by adding epoxy. Just a drop on the light side could help.
Jairus H. Watson
3/12/59-5/19/25
Requiescat in Pace
#107
Posted 29 October 2013 - 03:57 PM
"Already did that. Still slightly heavy on one side." See post # 104 and 105
I gotta move on, 2 more days off and I'm a little burned out on arms for now.
Next time, I'll get a drill press.
Paul Wolcott
#108
Posted 29 October 2013 - 06:14 PM
Back to familiar territory
Russkit bracket braced with rod.
This time, bushings will be soldered straight to the holes in the bracket, and custom brass tube spacers used to extend the rear wheels to 3".
For the jig, I'll use .185 tube pieces with .154 aluminum tubes inside. Slathered in ATF, they won't solder up. They will just be there to keep the bracket in place during the build. Bushings will be soldered home as one of the last steps. That way they will be perfectly aligned, and I don't have to worry about them moving around during the build. Rails will attach to the bracket only.
Paul Wolcott
#109
Posted 29 October 2013 - 06:19 PM
Can hear your sigh of relief as you get back to bending rod & soldering a Russkit bracket up Pablo
Anymore talk of armatures & rewinding could bring you out in a cold sweat
!
Bracket looks well braced
#110
Posted 29 October 2013 - 06:48 PM
I'll be back to arms, Paul, once I get Mr. Drill Press With a vengeance
Here is my method for aligning the bracket left to right before securing the rear axle works.
Flip the bracket down so the face is over the flag groove.
Then secure and flip back in place. re-check with calipers for perfect side to side alignment.
Paul Wolcott
#112
Posted 29 October 2013 - 07:07 PM
Ah yes Mr Drill Press! Another handy tool for making slot cars , which helps with many different parts of the process! One I will have to look into aswell
Nice lining up of the motor bracket
#113
Posted 29 October 2013 - 08:50 PM
Will this bracket be for another R&C chassis? Will it be a Can Am car since you already built a coupe & have an F1 in the works?
I intend to live forever! So far, so good.


#115
Posted 29 October 2013 - 09:09 PM
Hi Pablo,
Nice bracket! Remember though, the GP cars can only be 2 3/4" in wheel track width.
Rick Thigpen
Check out Steve Okeefe's great web site at its new home here at Slotblog:
The Independent Scratchbuilder
There's much more to come...
#116
Posted 29 October 2013 - 09:21 PM
Thanks Rick ! You saved me again !
2 3/4 it is.
I tried some tube bending experiments.
First is 063 tube with twin pieces of .087 tubes butted up against themselves.
Here was the result:
Next was the same as before, only with .032 wire inside the tube:
Result:
Paul Wolcott
#117
Posted 29 October 2013 - 09:24 PM
Nice smooth curve you got there Pablo! Amazing difference with that wire inside the tube Will have to try that with the SS tubing,
#118
Posted 29 October 2013 - 09:49 PM
In the second picture, the bend looks more uniform. I initially thought the two outside pieces of tubing were butted up againt one another. However, Steve Okeefe's writeup shows them spaced about 3/32" apart. I don't know yet how this spacing would affect the sharpness of a bend.
Paul E., what's the dia. of your JDS stainless tubing? In some photos, it looks like .065", yet in others, it looks larger. I'm not too sure how this bending process will work on stainless tubing. It could be too hard & need to be annealed before bending. But try it & see how it works.
I intend to live forever! So far, so good.


#119
Posted 29 October 2013 - 10:41 PM
Paul E.,
Bill is 100% correct (Hi, Bill); annealing is how I got the stainless tubing to bend so smoothly, and to the same radius as brass tubing, and with the same bending tools.
Nothing wrong with inserting piano wire like pablo did (Hi, Pablo) to prevent the tubing from collapsing or kinking, but if you use a good bending tool it should hardly be necessary!
Without annealing, you are going to have an awful time getting that stuff to bend for you at all (but I guess you already know that...) .
Someday I'm going to have to build another chassis using stainless steel tubing, but this time figure out how to do it without annealing or bending the tubing - that way I can capitalize on the hardened material's immense strength, stiffness and light weight.
Steve Okeefe
I build what I likes, and I likes what I build
#120
Posted 29 October 2013 - 10:47 PM
To avoid the major imbalance .... Bake the epoxy with the arm standing upright ... let the 'flow' run down into the Kevlar tie.
I used an 'oven' designed to 'cure' fiber optic connectors .... Works perfect but pricy.
Like this one --> http://www.specializ...-Oven-4426.aspx#
Just sayin how I did it.... you could do one at a time in the toaster oven buy standing the arm up in a .5xx drilled metal block or maybe even in an old motor can. The more mass around the stack the more even the heat will be. Toaster oven temp goes (cycles) up and down and not a very consistent, accurate or stable
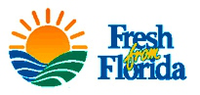
Bob Israelite
#121
Posted 29 October 2013 - 10:47 PM
Bill, the JDS SS tubing is indeed their .065" size
Oh Steve , I have found it can be pesky stuff to try and bend that's for sure!!! The K&S spring bender kit does an amazing job for what it cost, does some nice bends actually , although as noted probably won't bend tight without annealing.
Mr Havlicek bakes his armatures standing up in the easy bake oven ,allowing the epoxy to run down properly as you say Bob
:Update: Just tried the trick of bending the SS tube with the other larger pieces of tube over the top , very easy to bend actually ending up looking exactly as Pablo's first attempt at the brass tubing. Still looks pretty neat in the shiny SS and would probably make a nice looking "strong" chassis .
- Bill from NH likes this
#123
Posted 30 October 2013 - 05:27 PM

#124
Posted 30 October 2013 - 06:12 PM
I'm going to try something different for main rails. Steve OKeefe pioneered this method of bending 063 tubes using 3/32 tubes over it to produce nice smooth bends. Don Hollingsworth said, back in the day, they shoved wire into the tubes as well. So here is my new experiment. I'm going to leave the wire inside the tubes, and tack solder the ends. The wire can do whatever it wants inside the rails, flex, twist, warp, flop, etc. My extensive experience with .055 wire inside 093 square tubes for IRRA car rails leads me to believe this may result in an "interesting handler".
Step one: Tack wire to one end of the 063 tube.
Note the wire protrudes well beyond the end of the tube to allow for bending and heat.
.032 tube pieces are temporary handholds to bend the 063 tube:
Paul Wolcott